il progetto Amianto del CNR-IIA
Sviluppo di una metodologia innovativa per l’inertizzazione dell’amianto, abbattimento delle emissioni nocive e analisi di filiera complessiva
Convenzione
Il Ministero dell’Ambiente e della Tutela del Territorio e del Mare Direzione Generale per i Rifiuti e l’Inquinamento e l’Istituto sull’Inquinamento Atmosferico del Consiglio Nazionale delle Ricerche (CNR-IIA) hanno stipulato una convenzione in data 25 Novembre 2015 approvata con decreto RINDEC-20016-4 “Sviluppo di una metodologia innovativa per l’inertizzazione dell’amianto, abbattimento delle emissioni nocive e analisi di filiera complessiva”, le attività relative alla convenzione sono state avviate in data 6 Maggio 2016.
Le attività svolte in questa convenzione hanno permesso di migliorare e ampliare le conoscenze circa i processi di inertizzazione e la filiera dell’amianto, considerando questa prospettiva come metodologia di smaltimento dell’amianto.
Obbiettivi
L’obiettivo principale del progetto è quello di ottenere importanti dati progettuali e tecnologie adeguate allo scopo di maturare le conoscenze per poter definire una filiera per il trattamento dei rifiuti di amianto a scala industriale.
Allo stato dell’arte sono noti pochi esempi di utilizzo di sistemi la realizzazione di processi di inertizzazione di rifiuti di amianto e nessuno di questi è operativo su scala industriale, dunque occorre ampliare la conoscenza a riguardo.
In questo progetto sono stati studiati tutti gli aspetti riguardanti la filiera, dallo smaltimento al riutilizzo del materiale inertizzato, al fine di rendere l’intero processo un “ciclo chiuso”, cioè senza emissioni pericolose in atmosfera e senza la produzione di rifiuti di trattamento.
Per ottenere questo obiettivo si è realizzata una sperimentazione su scala di laboratorio, allo scopo di ottenere residui solidi innocui dall’arrostimento dei rifiuti tal quali, senza alcuna macinazione o preparazione.
Inoltre è stata definita la Filiera di inertizzazione e generalizzato il processo su scala industriale.
L’elemento centrale del progetto è quindi la realizzazione di un ciclo di trattamento che preveda l’abbattimento integrale delle emissioni gassose e il recupero totale dei materiali inerti.
i prodotti della ricerca
Monitoraggio delle emissioni su un prototipo
Il progetto si è focalizzato circa gli impatti che la funzionalità dell’ impianto potrebbe generare; dunque per ottenere tale obiettivo è stato eseguito un monitoraggio delle emissioni derivanti da un ciclo di trattamento di inertizzazione del cemento-amianto che si basa su un processo termico, la caratterizzazione dei sottoprodotti ottenuti e la successiva analisi energetica.
Le analisi sono state condotte su un prototipo, nello specifico sono state effettuate misurazioni per 5 diversi campioni, 3 dei quali avevano un contenuto di solo cemento-amianto ed altri 2 campioni composti da cemento-amianto e poliuretano, al fine di comprendere quali fossero le emissioni di un materiale composto non solo da cemento-amianto.
Le emissioni sono state monitorate con sistemi di misura on-line, e con sistemi di campionamento per analisi successive in laboratorio.
Le analisi on-line sono state effettuate tramite un analizzatore portatile multi-gas per le misure di NOx, SOx, CO, CO2 e un rilevatore paramagnetico per il rilevamento di ossigeno. Sono stati inoltre effettuati il campionamento per successiva analisi in laboratorio di composti organici volatili (VOC) e di microinquinanti associati alle polveri. I microinquinanti considerati sono i metalli, le diossine (PCDD/F), i policlorobifenili (PCB) e gli idrocarburi policiclici aromatici (PAH).
Inoltre è stato caratterizzato il materiale inerte derivato dal trattamento mediante analisi di Diffrazione di Raggi X (XRD)al fine di verificare l’effettiva inertizzazione dei campioni trattati
Confronto costi benefici fra diverse modalità di smaltimento
L’analisi condotta circa i costi e i benefici del processo di inertizzazione ha permesso di stimare dapprima i costi relativi alla realizzazione di un impianto di inertizzazione, i suoi costi di gestione, nonché i ricavi possibili derivati dalle entrate di smaltimento e di vendita del materiale inerte; e a seguire i benefici che il processo potrebbe apportare. Questi ultimi sono stati analizzati mettendo a confronto i benefici dell’inertizzazione rispetto alla dismissione in discarica, in termini di costi monetari e ambientali.
Analisi LCA (Life Cycle Assessment)
L’analisi LCA è volta a individuare gli impatti ambientali del processo di inertizzazione considerando tutte le fasi che compongono la filiera. Al fine di effettuare tale valutazione, sono stati utilizzati diversi metodi di valutazione dell’impatto.
L’analisi condotta ha permesso di valutare l’impatto LCA “Crandle to Gate” della filiera di trattamento del cemento-amianto da applicare in alternativa alla discarica.
Gli elementi in possesso e l’approccio dell’LCA hanno permesso di stimare in modo accurato le emissioni derivate dal trasporto e dall’impianto di inertizzazione nonché i prodotti e sottoprodotti in entrata e uscita del processo. Dunque la valutazione consente un buona stima dell’impatto relativo alle emissioni ma risulta poco indicativa circa la valorizzazione della trasformazione del cemento-amianto in materiale inerte.
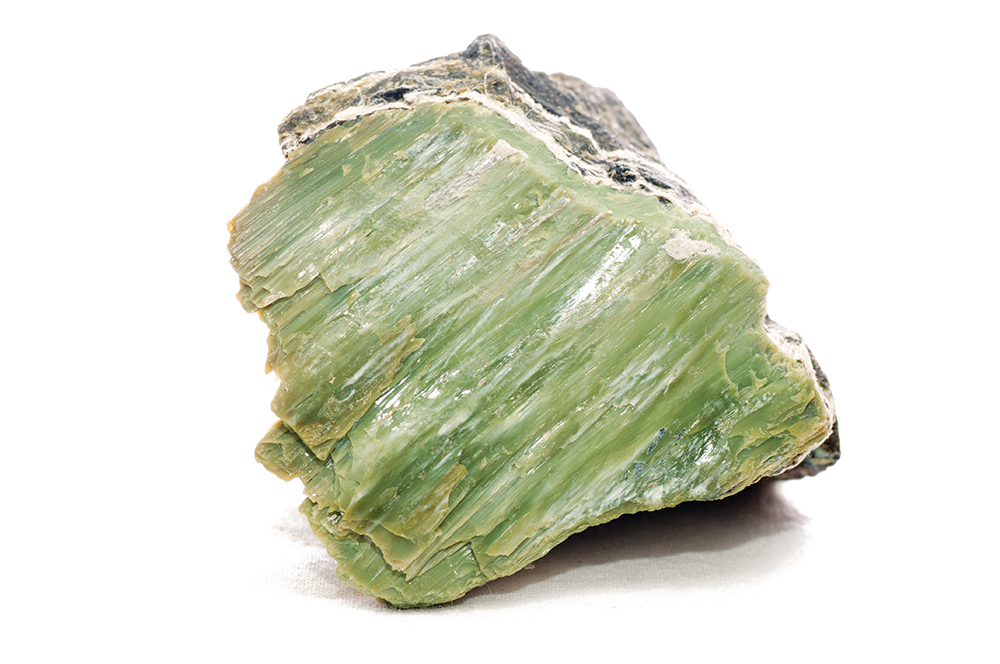
Le tecnologie di inertizzazione
Come indicato nella tabella B dell’Allegato A del Decreto 29 luglio 2004, n. 248 “Regolamento relativo alla determinazione e disciplina delle attività’ di recupero dei prodotti e beni di amianto e contenenti amianto” i processi di inertizzazione da poter applicare al fine di modificare completamente la struttura cristallochimica dell’amianto e dunque eliminare il pericolo connesso a tali materiali, sono i seguenti:
- modificazione chimica,
- modificazione meccanochimica,
- litificazione,
- vetrificazione,
- vetroceramizzazione,
- litizzazione pirolitica,
- produzione di clinker
- ceramizzazione
Il testo ammette anche la possibilità di introdurre nuove tecniche di inertizzazione, opportunamente verificate, e indica che le destinazioni finali dei materiali prodotti saranno analoghe a quelle dei materiali ottenuti con i trattamenti già noti.
I materiali sottoposti ad operazioni di trattamento, sono da considerare equivalenti ai materiali ottenuti da materie prime, qualora possiedano analoghe caratteristiche merceologiche per la loro commercializzazione ed impiego possono essere riutilizzati in altre filiere che necessitano di tali materiali.
Di seguito viene descritto l’attuale stato dell’arte sulle tecnologie di inertizzazione dei MCA, riportando i principi fisici su cui sono basate, i vantaggi e gli svantaggi.
Eseguendo una classificazione basata su principi fisici, tutti i processi considerati sono raggruppabili nelle seguenti 3 macrocategorie:
- Trattamenti termici – in cui si prevede una modifica della struttura cristallochimica ad elevate temperature
- Trattamenti chimici – in cui si prevede una modifica della struttura cristallochimica mediante l’applicazione di sostanze chimiche (acidi o basi forti concentrate)
- Trattamenti meccanochimici – in cui si prevede una modifica della struttura cristallochimica applicando la macinazione ad alta energia od una ultramacinazione
Trattamenti termici semplici
Nei processi di vetrificazione i MCA subiscono sono riscaldati a temperature generalmente superiori ai 1000 °C, al fine di ottenere un materiale siliceo inerte privo di fibre di amianto. A temperatura superiore ai 700 °C il desorbimento dell’acqua di cristallizzazione (strutturale) comporta un collasso della struttura cristallina fibrosa, con la conseguente produzione di un materiale vetroso inerte. Sulla base di questo fenomeno, alcuni processi di vetrificazione applicano ai MCA una temperatura attorno ai 900 °C, mentre in altri casi si raggiunge la fusione fino a 1300°C al fine di ottenere una massa fusa di silicati che raffredda danno origine a una massa vetrosa (in buona parte con strutture amorfe e priva di fibre di amianto) e scarsamente lisciviabile.
In generale, la criticità di tutti i trattamenti termici è legata alla modalità di riscaldamento del materiale. Forni elettrici e a metano sono generalmente utilizzati per raggiungere le temperature desiderate. Un alternativo metodo di riscaldamento molto efficiente ma molto dispendioso è rappresentato dal processo INERTAM (Morcenx, Francia) che utilizza per la fusione dei MCA una torcia al plasma (del tipo arc-discharge). La possibilità di degradare l’amianto usando un plasma ad arco, oltre ad essere confermata dalla applicazione pratica del processo INERTAM, è stata anche investigata e descritta dai lavori di Inaba e colleghi (Inaba et al., 1999; Inaba e Iwao, 2000).
In materia di modalità di riscaldamento particolari applicate alla vetrificazione, è utile citare anche il processo ideato da CEA (brevetto francese FR 2668.726; la licenza del brevetto è ceduta al gruppo industriale ONETT). Il processo si basa su un forno per induzione. Gli induttori sono costituiti da un solenoide alimentato in corrente ad alta frequenza (dai 200 ai 600 KHz) ottenuta da un generatore di 80 KW per un contenitore da 300 mm di diametro. La società DEFI-SISTEMES di Nimes ha proposto (domanda di brevetto n. 9607262) l’utilizzo di un forno ad alta frequenza, che richiede materiale conduttivo per alzare la temperatura. La I.N.P.G. Enterprise e il Politecnico di Grenoble hanno sviluppato un prototipo per il trattamento dell’amianto in cui si induce una “fusione magnetica ad alta frequenza”: il prototipo ha un serbatoio di 600 mm di diametro, 100 kV di potenza e 100 kHz di frequenza.
I processi di vetrificazione possono o meno prevedere dei pretrattamenti di triturazione e macinazione, che hanno lo scopo di diminuire le dimensioni, favorendo, così, la fusione dei materiali trattati. Generalmente sono anche presenti dei sistemi di abbattimento dei gas prodotti, che riducono le emissioni inquinanti in atmosfera. Ad esempio, la società VERT (Vitrification and Environmental Recycling Technology Limited) ha proposto il processo Mc Neill Vitrification Process (MVP), commercializzato attraverso la Chemical Exchange Directory s.a., con unità pilota installata nel 1996 nei pressi di Norimberga (Germania). Questo impianto pilota è interessante perché possiede un sistema di filtraggio delle emissioni, costituito da filtri in ceramica e torri di lavaggio con pH acido, alcalino e neutro. Esempio analogo è identificabile nel processo Vitrifix (brevetto europeo n. EP 0145.350A2 pubblicato nel 1985), in cui l’amianto è trattato 1350-1380 °C. Anche in questo caso è previsto un trattamento dei fumi (filtraggio e condensazione).
Un importante svantaggio della vetrificazione semplice per fusione è legato ai grandi costi di smaltimento del materiale prodotto, il quale, pur non essendo più nocivo, possiede poche applicazioni e deve essere spesso trattato come un rifiuto (non pericoloso). Tuttavia, se si identifica un settore di impiego per questo materiale, i costi dell’intero processo possono essere sensibilmente ridotti. possono essere ridotti.
Nell’ottica dell’utilizzo dell’inerte prodotto, è utile citare nuovamente il prototipo ideato da INPG e Politecnico di Grenoble, il cui inerte vetroso è utilizzabile per costruire strade e ripristinare cave. Anche il prodotto vetrificato finale del processo INERTAM (commercialmente noto come Cofalit) è sostanzialmente un basalto e viene utilizzato come inerte nella realizzazione di opere pubbliche. Sempre in materia di riutilizzo dell’inerte prodotto, si cita un processo di trattamento termico dell’amianto ideato da Italcementi, che prevede il trattamento a 600-800 °C con successiva reimmesso nel ciclo di produzione del cemento, come materia prima o correttivo in aggiunta per la produzione del clinker (Cucitore e Gilioli, 1992).
I processi analizzati che usano il trattamento della vetrificazione semplice per fusione descritti nel dettaglio nella Relazione sull’Analisi della Filiera sono i seguenti:
INERTAM
DENOMINAZIONE | DESCRIZIONE GENERALE | CARATTERISTICHE TECNICHE | FASI DEL PROCESSO |
INERTAM
PAESE: Francia BREVETTO EUROPEO: – TITOLARE: INERTAM/EUROPLASMA INVENTORE: – RICHIEDENTE: LICENZA: EDF/PROMETHÈE DATA DI PRIORITÀ: – DATA DI DEPOSITO: – DATA DI PUBBLICAZIONE: –
|
Vetrificazione semplice per fusione che utilizza il “plasma termico”, consistente in un gas parzialmente ionizzato, che, mediante un arco elettrico, viene portato ad una temperatura di 10000-12000 °C, sebbene l’amianto fonda ad una temperatura notevolmente inferiore.
Il processo è estremamente energivoro utilizzando una torcia al plasma di notevole potenza elettrica 1,75 MW e del tipo “arc discharge” o ad “arco trasferito”, la cui temperatura raggiunge i 4000-6000 °C, sebbene quella raggiunta dai RCA sia notevolmente inferiore e di circa 1600 °C. Tuttavia circa 1,435 MW sono recuperabili sotto forma di energia termica. Nel 1996, aveva una capacità di produzione di 4000 t/anno, portate poi a 8000 t con l’introduzione di una seconda torcia. La capacità di stoccaggio è di 2500 t di RCA sul sito. L’impianto tratta materiali, sia compatti che friabili, confezionati in mini bags, fusti metallici o big bags, direttamente caricati. Non si interviene con alcun additivo. Non tratta invece solventi, aerosol e materiali ad alto punto di fusione (refrattari ceramici, esplosivi, cartoni) ed i materiali ad alte concentrazioni di Pb, Zn, Hg e As. I fumi sono trattati con un postcombustore a 1100 °C e successivamente filtrati in due stadi (tra i sistemi di abbattimento degli inquinanti sono presenti, infatti, un elettrofiltro e delle torri di lavaggio). · |
CATEGORIA: termico.
SOTTOCATEGORIA: vetrificazione semplice per fusione con torcia al plasma. TEMPERATURA DI TRATTAMENTO: 1600 °C. STATO OPERATIVO: impianto operativo di Morcenx (Francia) attivo dal 1996 con capacità di 8000 t/anno, provvisto di due torce. MOBILITÀ: impianto fisso. ALIMENTAZIONE: elettrica. TIPO DI RCA TRATTABILE: compatti e friabili, esclusi materiali ad alto punto di fusione o alte concentrazioni di Pb, Zn, Hg e As. PRETRATTAMENTO: nessuno. MATERIALE INERTIZZATO: materiale vetrificato noto come COFALIT usato nella realizzazione di opere pubbliche, generalmente come riempimento per strade e massicciate ferroviarie. TRATTAMENTO REFLUI ED EMISSIONI: postcombustione dei fumi a circa 1200 per 2 s, successivo raffreddamento dei fumi a 170 con acqua e soda per neutralizzare le emissioni acide ed abbattimento delle polveri e dei metalli pesanti con elettrofili e filtri ad alta efficienza. |
· approntamento dei RCA sia compatti che friabili in mini bags, fusti metallici o big bags senza pretriturazione;
· fusione con una torcia al plasma; · colatura in siviere all’aria o direttamente in acqua per ottenere granulati; · trattamento dei fumi con un postcombustore a 1200 °C; · filtraggio in due stadi (elettrofiltro e torri di lavaggio). |
TERCA
DENOMINAZIONE | DESCRIZIONE GENERALE | CARATTERISTICHE TECNICHE | FASI DEL PROCESSO |
TERCA
PAESE: Italia BREVETTO ITALIANO: – BREVETTO EUROPEO: –TITOLARE: ENEA INVENTORE: – RICHIEDENTE: – RAPPRESENTANTE: – LICENZA: – DATA DI PRIORITÀ: – DATA DI DEPOSITO: – DATA DI PUBBLICAZIONE: –
|
· Processo di vetrificazione semplice per fusione mediante torcia al plasma.
· Esso prevede l’utilizzo di un sistema modulare ed intercambiabile per l’ottenimento di prodotti finali immediatamente riutilizzabili sotto forma di granulato inerte. I materiali friabili, non sottoposti ad alcun pretrattamento, vengono pesati e confezionati ed i prodotti finali utilizzati come riempimento per massicciate stradali. L’impianto che verrà assemblato e collaudato nel Mezzogiorno avrà una capacità di trattamento di 5 t/g. Non sono tuttavia noti i costi di trattamento.
|
CATEGORIA: termico.
SOTTOCATEGORIA: vetrificazione semplice per fusione. TEMPERATURA DI TRATTAMENTO: STATO OPERATIVO: impianto pilota. MOBILITÀ: mobile. ALIMENTAZIONE: – TIPO DI RCA TRATTABILE: friabili. PRETRATTAMENTO: nessuno MATERIALE INERTIZZATO: granulati utilizzati come riempimento per massicciate stradali. TRATTAMENTO REFLUI ED EMISSIONI: – |
· selezione, pesatura dei RCA e confezionamento;
· trattamento con torcia al plasma in forno; · colatura in acqua; · estrazione dei prodotti trasformati.
|
C.S.M.-ENEA
DENOMINAZIONE | DESCRIZIONE GENERALE | CARATTERISTICHE TECNICHE | FASI DEL PROCESSO |
C.S.M-ENEA
PAESE: Italia BREVETTO ITALIANO: BREVETTO EUROPEO: TITOLARE: C.S.M./ENEA INVENTORE: – RICHIEDENTE:- LICENZA: – DATA DI PRIORITÀ: – DATA DI DEPOSITO: – DATA DI PUBBLICAZIONE: –
|
· Processo di vetrificazione semplice per fusione.
· Si tratta di una versione mobile di capacità ridotta in grado di ottenere un prodotto riutilizzabile nell’industria del vetro o da impiegare per la produzione di lana di roccia. I materiali trattati sono friabili e vengono precedentemente macinati in un forno statico. Il costo di trattamento stimato è dell’ordine di 1200-1600 l/kg.
|
CATEGORIA: termico.
SOTTOCATEGORIA: vetrificazione semplice per fusione. TEMPERATURA DI TRATTAMENTO: STATO OPERATIVO: impianto pilota. MOBILITÀ: mobile. ALIMENTAZIONE: elettrica. TIPO DI RCA TRATTABILE: friabili e compatti. PRETRATTAMENTO: – macinazione ad umido dei RCA; · MATERIALE INERTIZZATO: prodotti riutilizzabili nell’industria del vetro o da impiegare per la produzione di lana di roccia. TRATTAMENTO REFLUI ED EMISSIONI: filtrazione secco/umido. |
· selezione e macinazione ad umido dei RCA;
· miscelazione con argilla principalmente caolino compreso tra il 55 e il 100% a temperature di 650 °C; · riscaldamento in forno ad una temperatura che varia tra i 650 e 1200 °C con primo passaggio ad uno stato amorfo della miscela iniziale e poi ottenimento di nuove fasi cristalline stabili; · colatura in acqua; · estrazione del materiale trasformato.
|
VERULTIM
DENOMINAZIONE | DESCRIZIONE GENERALE | CARATTERISTICHE TECNICHE | FASI DEL PROCESSO |
VERULTIM
PAESE: Francia BREVETTO EUROPEO: FR 2746037 A1 TITOLARE: – RICHIEDENTE: HERBERT JACQUES, FR e GUILHAUME PIERRE MANDANTE: BOETTCHER LICENZA: – DATA DI PRIORITÀ: – DATA DI DEPOSITO: 13/03/1996 DATA DI PUBBLICAZIONE: 19/09/1997
|
· Procedimento di vetrificazione semplice per fusione in forno a gas. Il forno è diviso in due sezioni:
– la prima è costituita da una camera di preriscaldamento, mantenuta a temperatura di 800-900 °C la quale consente la distruzione dei composti organici e la disidratazione dei MCA – la seconda è costituita dal forno di fusione vero e proprio dove si raggiungono temperature di 1400-1600 °C. Entrambe le due camere sono collegate tra di loro in modo tale che il cascame termico dei gas caldi generati all’interno della camera di fusione possa essere utilizzato all’interno della camera di preriscaldamento, recuperando in questo modo un‘ingente quantità di energia. Inoltre, il calore generato dai gas della camera di fusione, attraverso degli scambiatori di calore, è utilizzato per preriscaldare l’aria destinata agli inceneritori della camera di preriscaldamento fino a temperature che vanno dai 300 ai 500 °C. Per quanto riguarda la struttura della camera di fusione, essa è costituita da due parti: – una parte upstream (a monte) in cui i frammenti di metallo in forma solida e pastosa, presenti all’interno della matrice vetrosa, si sedimentano e vengono scaricati una volta compiuta l’opera di fusione. – una parte downstream (a valle) dove viene omogeneizzato il vetro ottenuto. In serie a questa sezione è presente un ulteriore comparto volto al trattamento finale del vetro. L’evacuazione del materiale è realizzata attraverso un dispositivo di colata tipo Verrier, seguito da uno stadio di granulazione in acqua del fuso. Un nastro trasportatore infine trasporta il vetro ottenuto in forma di granuli e lo scarica in una tramoggia apposita per la raccolta di rifiuti. L’installazione è completata da una sezione di trattamento dei fumi e dei gas comprendente una sezione di post-combustione, sezione di raffreddamento, filtraggio e lavaggio per la captazione di vapori acidi. Le polveri recuperate sono reintrodotte nel forno, mentre le acque residuali prodotte sono depurate per un loro completo riciclo. Tutto l’impianto è mantenuto in depressione per questioni di sicurezza. |
CATEGORIA: termico.
SOTTOCATEGORIA: vetrificazione semplice per fusione in forno a gas. TEMPERATURA DI TRATTAMENTO: 1400-1600 °C. STATO OPERATIVO: impianto pilota esistente ed uno in fase di sviluppo industriale. MOBILITÀ: fisso. ALIMENTAZIONE: bruciatore ossigeno-gas TIPO DI RCA TRATTABILE: friabili e materiali in forma eterogenea contenenti elementi inorganici, acqua, materiali combustibili e metallici. PRETRATTAMENTO: – macinazione dei RCA imballati in sacchi di plastica; – preriscaldamento a 800-900 °C per la distruzione dei composti organici e per la disidratazione. · MATERIALE INERTIZZATO: inerti utilizzabili nell’industria delle costruzioni. TRATTAMENTO REFLUI ED EMISSIONI: – post-combustione di fumi e gas; – sezione di raffreddamento, filtraggio e lavaggio per la captazione di vapori acidi; – polveri recuperate reintrodotte nel forno; – acque residuali prodotte depurate per un loro completo riciclo. |
· selezione, confezionamento e pesatura dei RCA;
· macinazione dei RCA in sacchi di plastica; · preriscaldamento e fusione in forno statico diviso in due sezioni; · colatura in acqua al fine di ottenere granulati.
|
MCNEILL VITRIFICATION
DENOMINAZIONE | DESCRIZIONE GENERALE | CARATTERISTICHE TECNICHE | FASI DEL PROCESSO |
MCNEILL VITRIFICATION
PAESE: Gran Bretagna BREVETTO EUROPEO: TITOLARE: VERT INVENTORE: – RICHIEDENTE: – LICENZA: Chemical Exchange Directory S.A. DATA DI PRIORITÀ: – DATA DI DEPOSITO: – DATA DI PUBBLICAZIONE: –
|
Vetrificazione semplice per fusione in forno a gas suddiviso in tre fasi:
– analisi dello scarto: questa fase permette di definire la composizione dello scarto e la sua variabilità composizionale nel tempo per ottimizzare la composizione della miscela adatta alla vetrificazione; – miscelazione: lo scarto industriale è miscelato con le materie prime come SiO₂, allumina (Al₂O₃), carbonato di magnesio (MgCO₃), carbonato di calcio (CaCO₃). Le proporzioni delle fasi minerali sono accuratamente controllate al fine di mantenere costante la composizione della miscela. Quest’ultima quindi viene trasferita in una tramoggia di stoccaggio ed introdotta automaticamente nel forno di fusione; – vetrificazione: questo stadio è realizzato in un forno a gas di forma rettangolare e rivestito di refrattari contenente il bagno di vetro fuso mantenuto a 1550 °C. Il contenuto organico della miscela subisce una pirolisi ed una decomposizione completa, mentre le frazioni minerali fondono e sono disciolte nel vetro. Al fine di consentire un tempo di combustione sufficiente della materia organica il forno è dimensionato in modo tale da ottenere, per i composti volatili, un tempo di residenza nella zona a 1550 °C di 2 secondi. Per assicurare una fusione completa del materiale ed una omogeneità di composizione il tempo di residenza della carica all’interno del forno è di circa 6 ore. Il vetro fuso è estratto mediante un dispositivo di colaggio posto sul fondo del forno stesso e raffreddato in un bacino di acqua fredda. |
CATEGORIA: termica.
SOTTOCATEGORIA: vetrificazione semplice per fusione in un forno a gas. TEMPERATURA DI TRATTAMENTO: 1550 °C. STATO OPERATIVO: pilota nei pressi di Norimberga nel 1996. MOBILITÀ: fisso mobile. ALIMENTAZIONE: elettrica. TIPO DI RCA TRATTABILE: materiali di diversa origine quali batterie, catalizzatori e filtri, scarti di lavorazione composti da residui metallurgici e scarti elettrolitici, scarti minerali, scarti organici e materiali fibrosi tipo lana di roccia, fibre di vetro ed amianto. PRETRATTAMENTO: miscelazione con additivi (silice, alluminia, carbonato di calcio, carbonato di magnesio). MATERIALE INERTIZZATO: granulati utilizzabili nell’industria delle costruzioni. TRATTAMENTO REFLUI ED EMISSIONI: emissioni gassose controllate attraverso un sistema di trattamento dei gas a recupero di calore. Il sistema di trattamento dei gas comprende un sistema di filtraggio in ceramica e delle torri di lavaggio in ambiente acido, alcalino e neutro. L’ultima fase è costituita da un raffreddamento del gas (70 °C) che provoca la condensazione del vapor d’acqua. L’acqua di condensazione e le acque di lavaggio sono trattate per essere riciclate nell’impianto o scaricate come acque municipali.
|
· selezione MCA;
· miscelazione con additivi (silice, alluminia, carbonato di calcio, carbonato di magnesio) per mantenere costante la composizione della miscela; · fusione in forno fusorio per vetro a 1550 °C per 6 ore; · colatura in acqua fredda (per ottenere granulati).
|
VITRIFIX
DENOMINAZIONE | DESCRIZIONE GENERALE | CARATTERISTICHE TECNICHE | FASI DEL PROCESSO |
VITRIFIX
PAESE: Gran Bretagna BREVETTO EUROPEO: EP 0145350 A2 TITOLARE: – INVENTORE: David Roberts, Henry Stuart Johnson MANDANTE: Cole, Paul Gilbert et al, Hughes Clark Byrne & Parker RICHIEDENTE: David Roberts, Henry Stuart Johnson LICENZA: – DATA DI PRIORITÀ: 21/11/1983 DATA DI DEPOSITO: 19/11/1984 DATA DI PUBBLICAZIONE: 19/06/1985
|
· Processo di vetrificazione semplice per fusione.
Il MCA in ingresso viene triturato per favorire il processo di fusione. In seguito viene aggiunto un basso-fondente quale ad esempio idrossido di sodio (soda caustica, NaOH, per inumidire le polveri derivanti dalla triturazione e per favorire principalmente l’incorporazione dell’amianto all’interno del vetro durante il processo di fusione. Successivamente, vengono aggiunti alla miscela di MCA e soda caustica degli scarti di vetro granulati (o alternativamente del materiale abitualmente utilizzato nella fabbricazione del vetro quale carbonati e sabbie). Il tutto viene infine inserito all’interno del forno elettrico a temperature intorno ai 1300-1400 °C. I tempi di residenza del materiale all’interno del forno sono circa di un’ora. Il vantaggio nell’utilizzo del forno elettrico e della soda caustica all’interno del processo è riscontrabile nella minore quantità di gas prodotti. Rispetto ad un forno che utilizza idrocarburi come carburante per produrre calore, il forno elettrico produce molti meno gas ed anche l’utilizzo della soda caustica rispetto ad esempio al carbonato di sodio provoca lo stesso effetto di ridurre i fumi durante la fase di fusione. Questo permette di risparmiare molto sul sistema di filtraggio dei fumi. Il vetro fuso infine viene scaricato all’interno di vasche di raffreddamento contenenti acqua per produrre granulati, utilizzabili principalmente nell’industria delle costruzioni. L’impianto pilota è interessante perché possiede un sistema di filtraggio delle emissioni, costituito da filtri in ceramica e torri di lavaggio con pH acido, alcalino e neutro. · |
CATEGORIA: termico.
SOTTOCATEGORIA: vetrificazione semplice per fusione. TEMPERATURA DI TRATTAMENTO: 1350-1380 °C. STATO OPERATIVO: impianto pilota. MOBILITÀ: fisso o mobile. ALIMENTAZIONE: elettrica. · TIPO DI RCA TRATTABILE: principali forme di amianto, i MCA sia compatti che friabili ed il cemento-amianto. PRETRATTAMENTO: – miscelazione insieme agli scarti di vetro granulati con aggiunta di piccole quantità di un basso-fondente come soda caustica (NaOH). MATERIALE INERTIZZATO: granulati utilizzabili nell’industria delle costruzioni TRATTAMENTO REFLUI ED EMISSIONI: – trattamento fumi con torri di lavaggio in ambiante acido, alcalino e neutro; – acque reflue trattate e riciclate. |
· selezione dei MCA;
· miscelazione con additivi e basso-fondenti; · aggiunta di vetro granulato(o alternativamente del materiale abitualmente utilizzato nella fabbricazione del vetro quale carbonati e sabbie); · fusione in forno elettrico tipo Verrier alla temperatura di 1350-1380 °C; · colatura in acqua fredda per ottenere granulati. |
CEA
DENOMINAZIONE | DESCRIZIONE GENERALE | CARATTERISTICHE TECNICHE | FASI DEL PROCESSO |
CEA
PAESE: Francia BREVETTO EUROPEO: FR 2668726 A1 TITOLARE: CEA (Commissariat à l’énergie atomique et aux énergies alternatives) INVENTORE: Jouan A., Boen R., Largillier JJ.e L. H. Pilliol RICHIEDENTE: CEA (Commissariat à l’énergie atomique et aux énergies alternatives) LICENZA: gruppo industriale ONETT DATA DI PRIORITÀ: DATA DI DEPOSITO: 2/11/1990 DATA DI PUBBLICAZIONE: 7/05/1992
|
· Meccanismo di vetrificazione semplice per fusione mediante un forno elettrico a crogiolo freddo e ad induzione diretta ad alta frequenza.
Gli induttori, costituiti da solenoidi alimentati con una corrente ad alta frequenza compresa tra i 200 ed i 600 kHz ed ottenuta da un generatore di 80 kW, sono disposti attorno ad un crogiolo freddo. Il crogiolo, in metallo (rame, acciaio inossidabile ecc..), ha un diametro di 300 mm ed è raffreddato ad acqua. Al fine di diminuire la temperatura di fusione della miscela contenente amianto viene aggiunto, in minima quantità, un basso-fondente aggressivo come il borace noto anche come tetraborato di sodio (Na2B4O7). Il basso-fondente viene utilizzato per lo più quando la temperatura diventa troppo elevata e raggiunge ad esempio i 1600 °C. L’amianto fuso genera una massa vetrosa che viene continuamente scaricata attraverso un ugello localizzato sul fondo del contenitore, sormontato da una campana che impedisce alle fibre d’amianto non ancora fuse di passare attraverso il foro. La temperatura raggiunta dal forno coincide con la temperatura di fusione dei composti, variabile questa a sua volta a seconda della tipologia di minerale d’amianto considerato e del basso-fondente aggiunto. Il dispositivo prevede un sistema di raffreddamento e una camera di post-combustione dove vengono bruciati gli eventuali composti organici volatili derivanti dalla fusione. I gas uscenti dal camino vengono in seguito lavati e filtrati per evitare l’aerodispersione delle fibre. L’impianto di piccole dimensioni e mobile tratta materiali friabili ed i prodotti finali granulati sono utilizzabili nell’industria delle costruzioni. |
. CATEGORIA: termico.
SOTTOCATEGORIA: vetrificazione semplice per fusione. TEMPERATURA DI TRATTAMENTO: 1600 °C. STATO OPERATIVO: laboratorio. MOBILITÀ: mobile. ALIMENTAZIONE: elettrica. TIPO DI RCA TRATTABILE: friabili. PRETRATTAMENTO: – aggiunta di un basso-fondente come il borace utilizzato per lo più quando la temperatura diventa troppo elevata e raggiunge ad esempio i 1600 °C. MATERIALE INERTIZZATO: granulati utilizzabili nell’industria delle costruzioni. TRATTAMENTO REFLUI ED EMISSIONI: – lavaggio e filtraggio; – acque reflue trattate e riciclate.
|
· selezione dei MCA;
· miscelazione con basso-fondenti come il borace; · fusione in forno elettrico ad induzione a 1600 °C; · colatura in acqua fredda per ottenere granulati.
|
DÉFI-SYSTÈMES
DENOMINAZIONE | DESCRIZIONE GENERALE | CARATTERISTICHE TECNICHE | FASI DEL PROCESSO |
DÉFI-SYSTÈMES
PAESE: Francia BREVETTO EUROPEO: FR 2749523 A1 TITOLARE: – INVENTORE:- RICHIEDENTE: Patrick Curie LICENZA: – DATA DI PRIORITÀ: – DATA DI DEPOSITO: 6/6/1996 DATA DI PUBBLICAZIONE: 12/12/1997
|
· Processo di vetrificazione semplice per fusione mediante un forno elettrico ad alta frequenza.
Il processo consiste nel fondere le fibre di amianto all’interno di un crogiolo in alluminio tramite l’azione di un campo elettromagnetico ad una frequenza compresa tra i 30 ed i 300 MHz. utilizzando un generatore di non elevata potenza (3 kW). L’isteresi dielettrica che si verifica all’interno delle fibre, genera un’energia che fa fondere quest’ultime in tempi molto brevi, dell’ordine dei minuti. Le prove effettuate, hanno dimostrato che una massa di amianto di volume pari a 0,1 L, a 64 MHz e ad una potenza di 3 kW, in soli dieci minuti, fonde. Per frequenze minori di 27 MHz e potenze di 40 KW la massa non fonde. A seguito di questo trattamento l’amianto analizzato al microscopio a scansione risulta privo del proprio abito fibroso e della propria morfologia. Al fine di diminuire l’energia necessaria alla fusione delle fibre, vengono aggiunti, in qualità di basso-fondenti, degli additivi, come ad esempio il sodio (sale di mare). L’involucro termico, al termine del processo, include anche composti organici volatili, derivanti dalla fusione delle fibre.
|
CATEGORIA: termico.
SOTTOCATEGORIA: vetrificazione semplice per fusione. TEMPERATURA DI TRATTAMENTO: STATO OPERATIVO: impianto pilota. MOBILITÀ: fisso o mobile. ALIMENTAZIONE: elettrica. TIPO DI RCA TRATTABILE: friabili. PRETRATTAMENTO: – aggiunta di un basso-fondente come il sodio. MATERIALE INERTIZZATO: granulati utilizzabili nell’industria delle costruzioni. TRATTAMENTO REFLUI ED EMISSIONI: – |
· selezione dei MCA:
· miscelazione con basso-fondenti come il sodio; · fusione in forno elettrico ad alta frequenza; · colatura in acqua fredda per ottenere granulati.
|
MODYAM
DENOMINAZIONE | DESCRIZIONE GENERALE | CARATTERISTICHE TECNICHE | FASI DEL PROCESSO |
MODYAM
PAESE: Italia BREVETTO ITALIANO: – BREVETTO EUROPEO: – TITOLARE: Aspireco S.r.l. INVENTORE: – MANDANTE: – LICENZA: – DATA DI PRIORITÀ: – DATA DI DEPOSITO: – DATA DI PUBBLICAZIONE: –
|
Processo che si basa sulla trasformazione termica dell’amianto, sia in lastra che friabile, mediante un processo di deossidrilazione (ossia di eliminazione dell’acqua strutturale), in un forno rotante a metano, mantenuto costantemente in depressione e successiva ricristallizzazione chimica allo stato solido nel minerale forsterite (un silicato di Mg non pericoloso per l’uomo) a 1000-1300 °C, ottenuta in un tempo di tre/quattro ore.
Il materiale, imballato sui pallets, viene appositamente granulato ed inviato al forno. Quello che si ottiene dal processo è un “filler”, ossia un materiale pulverulento inerte. |
CATEGORIA: termico.
SOTTOCATEGORIA: trattamento termico a media temperatura. TEMPERATURA DI TRATTAMENTO: 1100 °C. STATO OPERATIVO: impianto pilota e operativo ad Arborea. MOBILITÀ: fisso e mobile. ALIMENTAZIONE: metano. TIPO DI RCA TRATTABILE: compatti e friabili su pallets PRETRATTAMENTO: – macinazione dei RCA imballati su pallets. MATERIALE INERTIZZATO: si ottiene un “filler”, ossia un materiale pulverulento inerte, riutilizzabile per uso edilizio nelle malte, nei conglomerati bituminosi, in sottofondi stradali e nella produzione del cemento. TRATTAMENTO REFLUI ED EMISSIONI: filtrazione secco/umido. |
· macinazione dei RCA imballati su pallets;
· stivaggio; · invio del materiale macinato in un forno rotante a metano mantenuto in depressione a 1100 °C; · ricristallizzazione chimica a 1000-1300 °C nel minerale forsterite in un forno primario; · stabilizzazione del materiale a 950 °C in un forno secondario; · scarico forno e stoccaggio materiale trasformato; · ulteriore macinazione mediante mulino a sfere per ridurre il materiale trattato alle dimensioni del filler per uso edilizio, malte, conglomerati bituminosi, sottofondi stradali, produzione del cemento. |
NIAL NIZZOLI
DENOMINAZIONE | DESCRIZIONE GENERALE | CARATTERISTICHE TECNICHE | FASI DEL PROCESSO |
NIAL NIZZOLI
PAESE: Italia BREVETTO ITALIANO: – BREVETTO EUROPEO: – TITOLARE: NIAL NIZZOLI S.r.l., Correggio (RE) INVENTORE:- RICHIEDENTE:- LICENZA: – DATA DI PRIORITÀ: – DATA DI DEPOSITO:- DATA DI PUBBLICAZIONE: –
|
Pirolisi in un forno lineare a metano con temperatura di cottura di 1150 °C e per una durata complessiva di 10-40 minuti.
I RCA imballati su pallets vengono aperti e le lastre inviate singolarmente al forno. |
CATEGORIA: termico.
SOTTOCATEGORIA: TEMPERATURA DI TRATTAMENTO: 1150 °C. STATO OPERATIVO: impianto pilota. MOBILITÀ: fisso. ALIMENTAZIONE: metano. TIPO DI RCA TRATTABILE: compatti. PRETRATTAMENTO: nessuno. MATERIALE INERTIZZATO: materiale finale utilizzato per l’esecuzione di sottofondi stradali, come additivo per materiali ceramici, refrattari, adesi, sigillanti e materie plastiche. TRATTAMENTO REFLUI ED EMISSIONI: filtrazione secco/umido. |
· introduzione dei RCA imballati su pallets che vengono aperti ed inviati direttamente ad un forno lineare a metano mantenuto in depressione ad una temperatura di 1150 °C e per una durata complessiva di 10-40 minuti;
· estrazione dei prodotti trattati. |
TCCT
DENOMINAZIONE | DESCRIZIONE GENERALE | CARATTERISTICHE TECNICHE | FASI DEL PROCESSO |
TCCT
PAESE: Gran Bretagna/Stati Uniti BREVETTO: TITOLARE: ARI Global Technologies, Inc INVENTORE: – RICHIEDENTE: – LICENZA: – DATA DI PRIORITÀ: – DATA DI DEPOSITO: – DATA DI PUBBLICAZIONE: –
|
Processo termico che prevede un pretrattamento chimico e successivamente l’utilizzo di calore, con successiva rimineralizzazione degli asbesti in nuove fasi silicatiche e senza che avvenga fusione.
Essi vengono frantumati in frantoio con conseguente riduzione delle dimensioni, inferiori ai 25 mm. Seguono ulteriori fasi di frantumazione ed un pretrattamento basico mediante una soluzione alcalina al 5-7% di borace come agente mineralizzante o basso-fondente. Il tutto viene poi convogliato per 20 minuti in un forno rotativo mantenuto alla temperatura di 1200 °C, il quale presenta un’alimentazione di 300 kg/h di materiale da trattare. Il prodotto risultante viene così versato in una vasca contenente acqua, estratto e trasferito in un recipiente di stoccaggio. Nel forno vengono introdotti circa 600 kg/h di aria per trattare i composti organici e i vapori sono trattati con soluzioni di soda. I gas vengono raffreddati prima di essere scaricati in atmosfera mediante un filtro HEPA. Il risultato è la formazione di nuovi minerali vulcanici non più fibrosi quali olivina, wollastonite, diopside ed altri pirosseni, nonché piccole quantità di vetro laddove la fusione è incominciata. |
CATEGORIA: termico.
SOTTOCATEGORIA: trattamento termico con pretrattamento basico. TEMPERATURA DI TRATTAMENTO: 1200 °C. STATO OPERATIVO: impianto pilota/prototipo industriale. MOBILITÀ: fisso e mobile. ALIMENTAZIONE: elettrico o a metano. TIPO DI RCA TRATTABILE: compatti o friabili/amianti in matrici organiche in big bags. PRETRATTAMENTO: – macinazione dei RCA; – miscelazione con soluzione alcalina al 5/7% (flussaggio in soluzione basica). MATERIALE INERTIZZATO: materiali per l’industria delle costruzioni e per sottofondi stradali, granulati per il calcestruzzo, fertilizzanti o stabilizzanti dei suoli. TRATTAMENTO REFLUI ED EMISSIONI: – vapori sono trattati con soluzioni di soda; – gas raffreddati prima di essere scaricati in atmosfera mediante un filtro HEPA.
|
· macinazione dei RCA con frantoio;
· miscelazione con una soluzione alcalina al 5/7% di borace come agente mineralizzante; · trattamento in forno rotativo per 20 minuti mantenuto in depressione; · raffreddamento in una vasca contenente acqua; · estrazione dei prodotti.
|
In alcuni casi, i trattamenti termici possono essere condotti con l’eventuale aggiunta di additivi o basso-fondenti, in diverse percentuali ed in genere alcalini, come ad esempio la soda caustica (NaOH) o l’idrossido di potassio (KOH), aventi lo scopo di diminuire la temperatura di fusione dei minerali asbestoidi. Nel caso in cui tali reattivi siano aggiunti con lo scopo di idrolizzare il legame Si-O delle fibre di amianto, si rimanda ai trattamenti chimici.
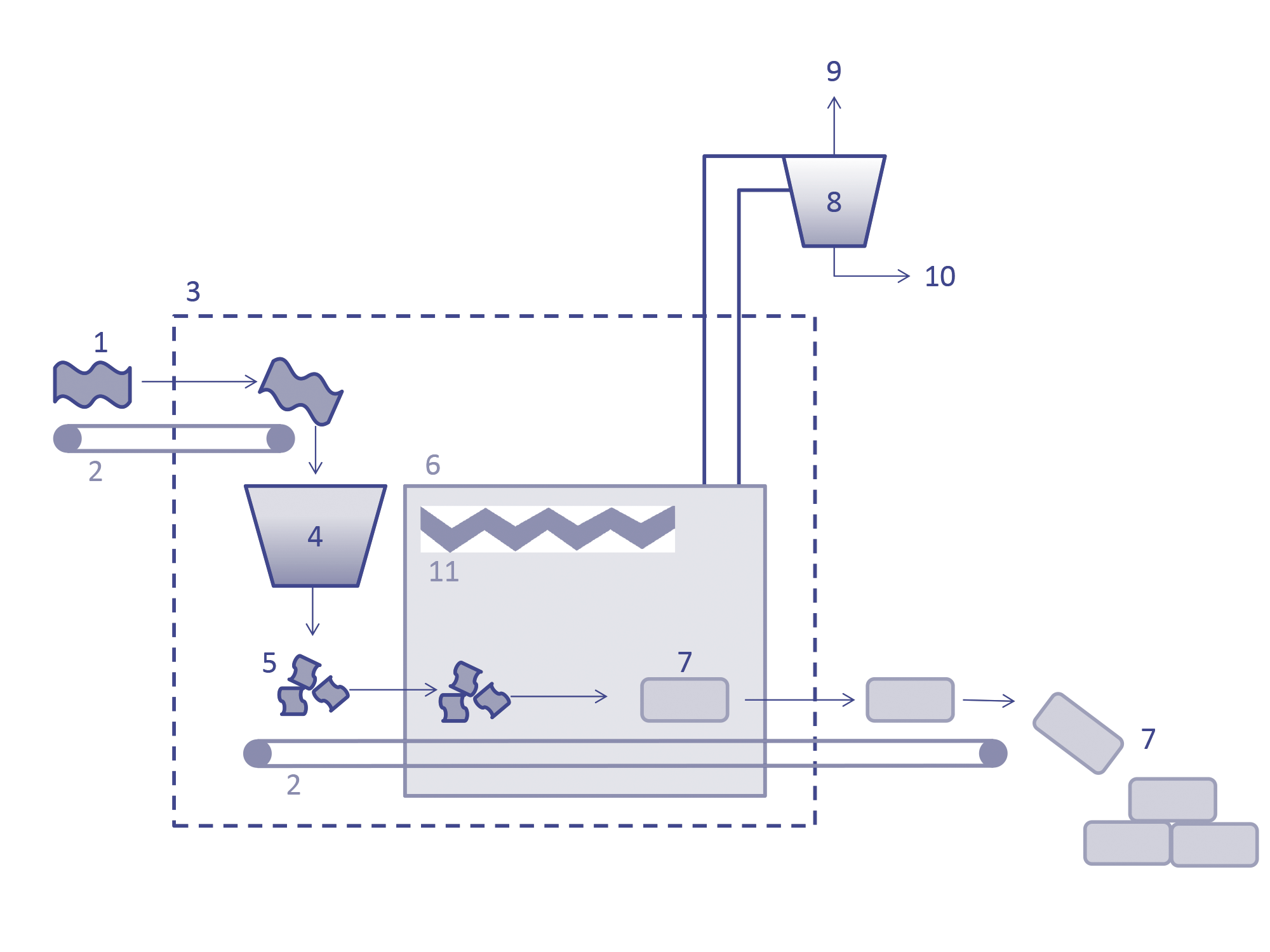
Diagramma di flusso del trattamento termico di MCA (sia vetrificazione semplice sia ricristallizzazione controllata), ingresso MCA grezzi (1), nastri trasportatori (2), zona di bassa pressione (3), frantoio (4), MCA frantumato (5), zona ad alta temperatura (6), materiale inerte (7), sistema di abbattimento delle emissioni (8), emissioni di gas di scarico nell’atmosfera (9), ceneri (10) e fonte di calore (11).
Trattamenti termici con ricristallizzazione controllata
Se dopo la fusione si fa avvenire una ricristallizzazione a temperatura controllata, è possibile ottenere prodotti con buone proprietà meccaniche, utilizzabili in opere edili o civili. In base al trattamento termico specifico, si parla di vetroceramizzazione, ceramizzazione e litificazione.
I trattamenti termici di vetroceramizzazione si basano su un processo di fusione ad elevata temperatura. Tale fase avviene ad una temperatura compresa tra i 1350 ed i 1550 °C. Segue una fase di omogeneizzazione del fuso, una detta di nucleazione, a temperatura più bassa della precedente e compresa tra i 700 ed i 900 °C ed una fase finale di cristallizzazione, durante la quale si forma la componente cristallina del vetroceramico, a temperature comprese tra i 750 ed i 950 °C. I tempi di fusione, nucleazione e cristallizzazione sono lunghi e dipendono dalla fluidità del fuso, dalle condizioni di degassaggio del materiale di partenza e dal tipo di lavorabilità che deve avere il materiale finale.
Nei processi di litificazione, alla fase di fusione segue una fase di parziale cristallizzazione ottenuta per lento raffreddamento che determina la produzione di un materiale duro e ad elevato peso specifico con ottima resistenza meccanica alla compressione e alla trazione per il 75% interno di natura vetrosa e per il 25% esterno di natura cristallina. Tipicamente, nella litificazione la fusione avviene a temperature comprese tra 1300-1450 °C.
In questa sottocategoria di trattamenti si concentrano la maggior parte dei brevetti sull’inertizzazione dell’amianto. Tipicamente, nelle rivendicazioni di questi brevetti viene protetto sia il processo che il materiale ottenuto. La conversione termica dell’amianto in materiali ceramici è stata inoltre descritta nelle ricerche condotte presso l’Università di Modena e Reggio Emilia (Gualtieri e Tartaglia, 2000; Gualtieri et al., 2008, 2012).
Applicando tali processi, si osserva la completa conversione cristallochimica dei minerali asbestoidi per processi di deidrossilazione (o perdita di acqua strutturale) e successiva modifica strutturale in fasi non più pericolose di differente tipologia, analogamente ai processi di vetrificazione. Tuttavia, i materiali ottenuti con i processi di vetroceramizzazione/litificazione sono a loro volta materiali con interessanti proprietà meccaniche, come ad esempio la cordierite, materiale ceramico pregiatissimo, utilizzata come refrattario e supporto ceramico per la fabbricazione delle marmitte catalitiche e di filtri catalitici per uso industriale. Altri prodotti minerali possono essere la forsterite, l’enstatite, la cristobalite ed il periclasio. I materiali ceramici formatisi sono a basso coefficiente di espansione termica, risultano totalmente privi di fibre di amianto e non posseggono più la struttura fibrosa iniziale, ma una di tipo colonnare, non più inspirabile. I seguenti processi di ceramizzazione sono analizzati nel dettaglio nella Relazione Tecnica sull’Analisi della Filiera degli MCA, realizzata contestualmente a questo studio:
KRY-AS
DENOMINAZIONE | DESCRIZIONE GENERALE | CARATTERISTICHE TECNICHE | FASI DEL PROCESSO |
KRY-AS
PAESE: Italia BREVETTO ITALIANO: MO2006A000205 BREVETTO EUROPEO: EP 2027943 A1/B1 TITOLARE: INVENTORE: Alessandro Francesco Gualtieri e Ivano Zanatto del Dipartimento di Scienze della Terra dell’Università di Modena e Reggio Emilia in collaborazione con la società ZETADI S.r.l. RICHIEDENTE: Ivano Zanatto RAPPRESENTANTE: – LICENZA: – DATA DI PRIORITÀ: 31/07/2007 DATA DI DEPOSITO: DATA DI PUBBLICAZIONE: 25/02/2009
|
Processo di trasformazione termica mediante ceramizzazione dei RCA utilizzando un forno continuo.
Il trattamento non prevede alcuna macinazione prima della cottura e i big bags contenenti lastre di cemento-amianto rimangono, quindi, sigillati in modo tale da evitare il rilascio di fibre. Il ciclo di cottura utilizza un forno industriale continuo “a tunnel” alimentato a metano, generalmente utilizzato per la produzione di laterizio, di lunghezza non inferiore a 50 m. Il processo (combustione dei big bags, disidratazione, decarbonatazione e deossidrilazione) prevede un riscaldamento alla temperatura massima di 1200-1300 °C per non più di 8 ore. In seguito, il materiale viene immesso in una zona di cottura alla medesima temperatura per circa 12 ore ed infine raffreddato per circa 6 ore in una sezione del forno a 25 °C. |
CATEGORIA: termico.
SOTTOCATEGORIA: ceramizzazione. TEMPERATURA DI TRATTAMENTO: 1200-1300 °C. STATO OPERATIVO: impianto pilota. MOBILITÀ: fisso. ALIMENTAZIONE: metano. TIPO DI RCA TRATTABILE: compatti e friabili. PRETRATTAMENTO: nessuno. MATERIALE INERTIZZATO: KRY-AS (dal greco krustallos KR e asbeston AS, letteralmente “cristalli dagli asbesti”), un materiale a matrice silicatica formato da una miscela di silicati di Ca, Mg, Al e Fe, quali akermanite, ferrite e merwenite. Si produce anche una consistente quantità di vetro pari a circa il 29%. Tale miscela ha una composizione assimilabile a quella di un clinker grigio e viene macinato a secco, omogeneizzato ed utilizzato come additivo, in diverse percentuali (dal 10 al 40%), per produrre materie plastiche, vetro, calcestruzzo, fritte ceramiche, cemento, smalti e pigmenti inorganici ceramici tra cui uno a base di uvaruvite verde ed un altro a base malayaite rosa, quest’ultimo interessante come sostituto per pigmenti a base di Cd ed ancora nella fabbricazione di tegole e mattoni e di lana di roccia e vetro. TRATTAMENTO REFLUI ED EMISSIONI: impianto è dotato di un sistema di post-combustione attraverso il quale vengono ulteriormente ossidate le eventuali fibre presenti all’interno dei gas di scarico. |
· prima fase della durata non inferiore alle 8 ore con un riscaldamento fino alla temperatura di cottura di 1200-1300 °C nella zona di precottura del forno a tunnel;
· seconda fase della durata non inferiore alle 12 ore alla temperatura massima di cottura di 1200-1300 °C nella zona di cottura del forno a tunnel; · terza fase della durata non inferiore alle 6 ore con un lento raffreddamento nella zona di raffreddamento del tunnel; · produzione del materiale; · macinazione finale del prodotto. |
ASBESTEX
Il processo può avvenire anche con un’eventuale aggiunta di additivi, quali scorie di altoforno o fanghi industriali, come i fanghi rossi, ovvero reflui provenienti dall’estrazione elettrolitica dello zinco, che conferiscono al materiale un alto tenore in metalli: in tal caso si rimanda al successivo paragrafo.
Trattamenti termici in presenza di altri materiali inorganici
Al fine di migliorare le proprietà e le possibilità di utilizzo dell’inerte prodotto, oltre alle ricristallizzazioni controllate, è possibile ricorrere all’aggiunta di materiali inorganici come le argille. Tale approccio non va tuttavia confuso con l’aggiunta di agenti chimici che hanno lo scopo di reagire direttamente con le fibre di amianto: in in tal caso si tratterebbe infatti di trattamenti chimici.
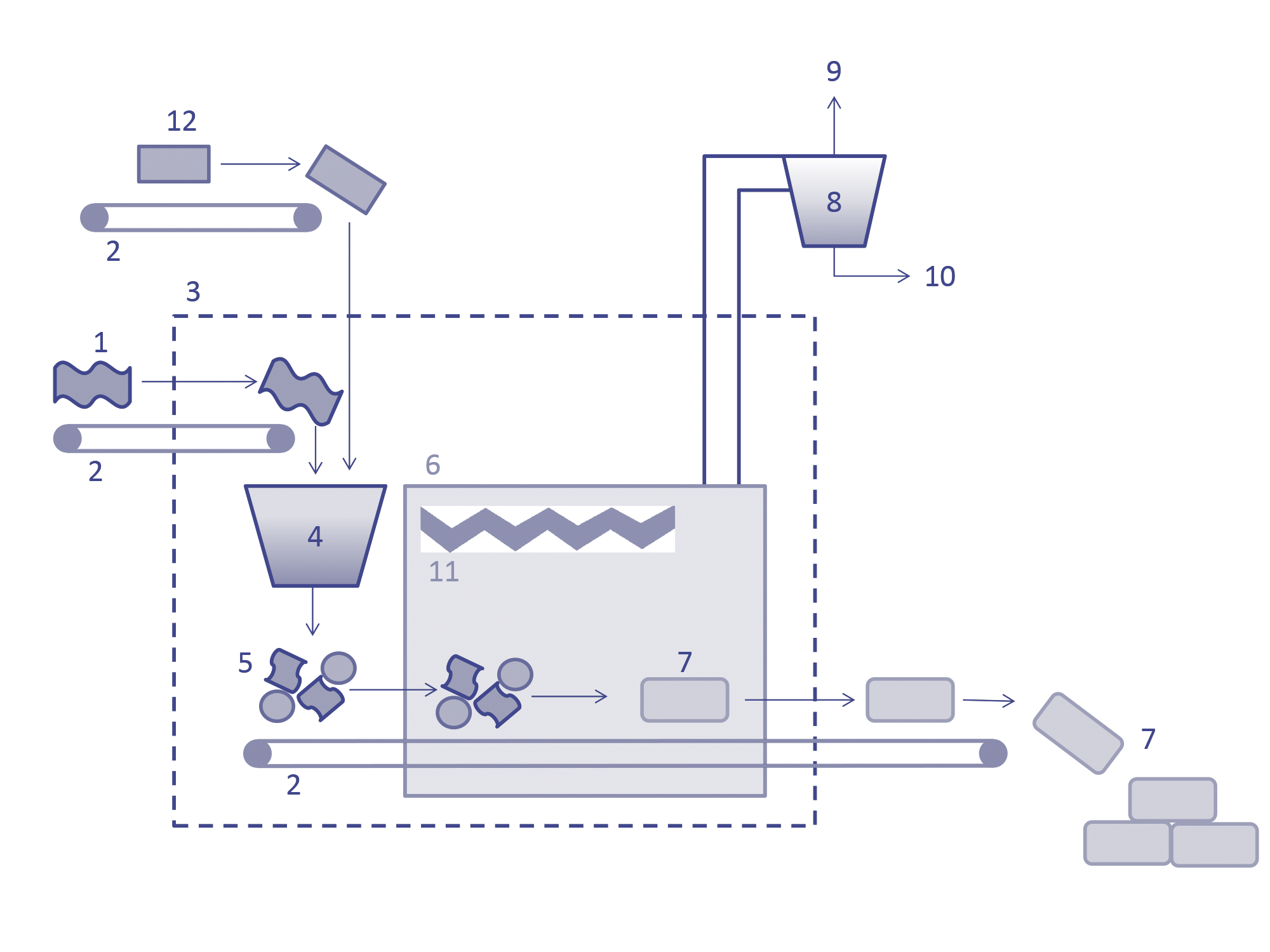
Diagramma di flusso del trattamento termico in presenza di altri materiali inorganici – ingresso MCA grezzi (1), nastri trasportatori (2), zona di bassa pressione (3), frantoio (4), MCA frantumato e miscelato con altri materiali inorganici (5), zona ad alta temperatura (6), materiale inerte (7), sistema di abbattimento delle emissioni (8), emissioni di gas di scarico nell’atmosfera (9), ceneri (10), fonte di calore (11)
La cosiddetta “litifizzazione pirolitica” (da non confondersi con la litificazione descritta nel precedente paragrafo 2.2) porta i MCA a essere miscelati con argilla e impiegati nella produzione di argilla espansa: a una fase di essiccazione a 300°C con perdita dell’acqua di costituzione, seguono fasi di combustione a 1.000°C (in presenza di sostanze organiche), di fusione parziale a 1.300°C e successiva vetrificazione solo delle parti esterne dei granuli a base di argilla che non fondono completamente a causa della bassa conducibilità termica del materiale lasciando adeguate porosità all’interno. L’elevata reattività dell’argilla a 650-950° C favorisce l’integrazione di fasi silicatiche apportate dai RCA.
In questa sottocategoria di processi rientra il processo CORDIAM (Brevetto RM96A000782), sviluppato dall’Istituto Trattamento dei Minerali del CNR, descritto nel dettaglio nella Relazione sull’analisi della filiera. In alternativa all’argilla, il Centro ricerche e valorizzazione residui dell’ENEL (brevetto n. MI98A002194) ha proposto l’uso di ceneri leggere di carbone, in un ciclo termico di fusione a circa 1200°C per un’ora. Entrambi questi processi sono descritti dettagliatamente nella relazione sull’Analisi della Filiera.
Il processo della Italcementi precedentemente descritto può sotto alcuni aspetti essere considerato come un ulteriore esempio di questo approccio: infatti, il MCA viene preliminarmente trattato a 600-800 °C e in seguito miscelato ad altre componenti inorganici nella fase di preparazione del clinker.
Trattamenti con microonde
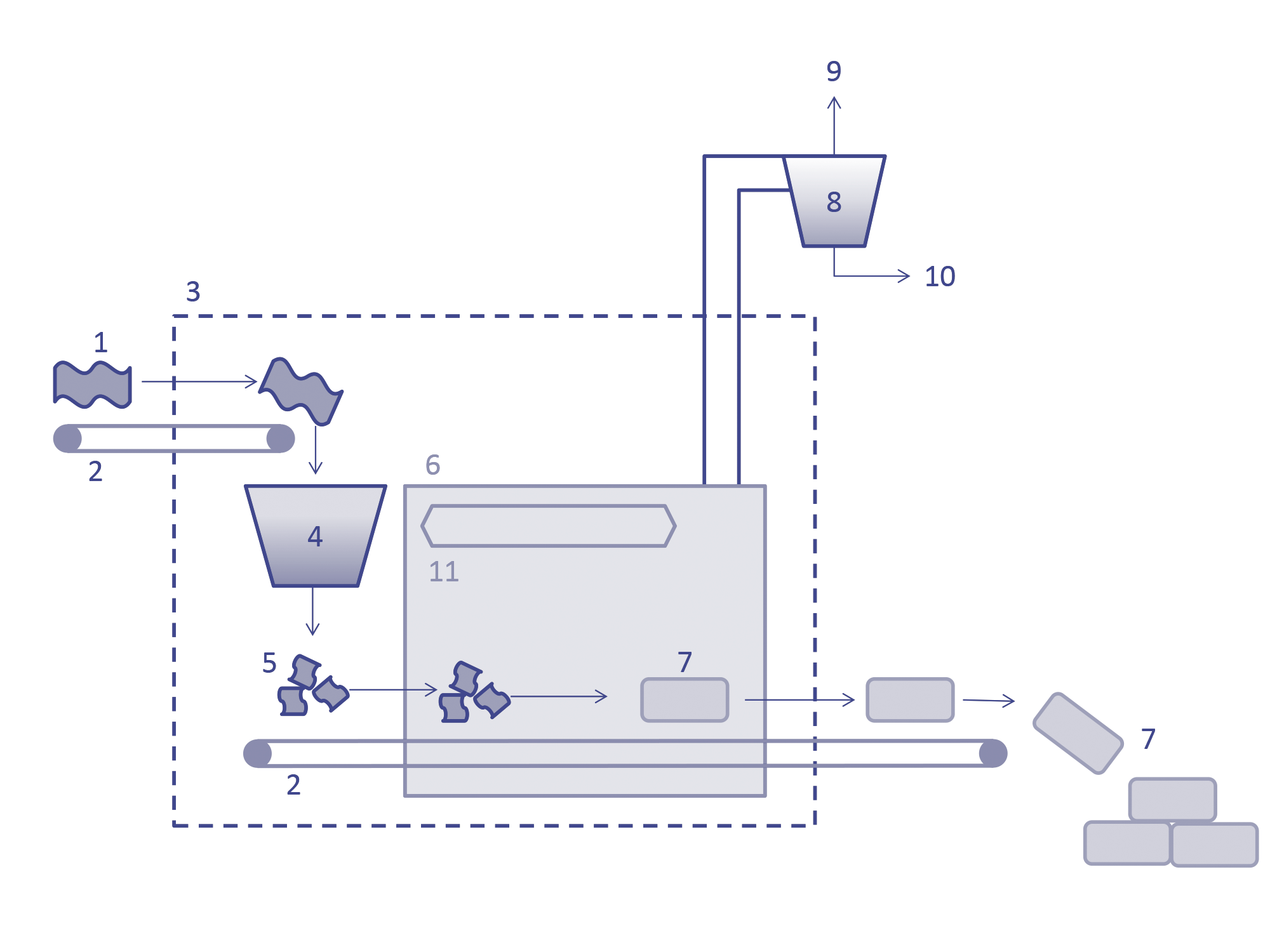
Diagramma di flusso del trattamento termico di MCA con microonde, ingresso MCA grezzi (1), nastri trasportatori (2), zona di bassa pressione (3), frantoio (4), MCA frantumato (5), zona ad alta temperatura (6), materiale inerte (7), sistema di abbattimento delle emissioni (8), emissioni di gas nell’atmosfera (9), ceneri (10) e sorgenti di microonde (11).
Al fine di trasmettere in maniera efficiente il calore, è stata investigata la possibilità di utilizzare le microonde. È stato infatti dimostrato (Leonelli et al., 2006) che è possibile aggiungere i MCA alla ceramica (fino al 5%) e successivamente convertire la miscela in forsterite tramite riscaldamento con microonde.
Le microonde possono inoltre essere utilizzate per generare un plasma di aria in grado di raggiungere i 3000 °C con la conseguente inertizzazione dell’amianto per fusione e successiva vetrificazione; l’efficienza del processo sembra aumentare all’aumentare del rapporto allumio/silicio (Averroes et al., 2011). Come suggerito da Horikoshi et al. (2014), l’efficienza delle microonde nel trattamento dell’amianto può essere ricondotta alla maggior penetrazione del calore e all’incremento dell’intensità del campo elettrico tra le fibre. Nel caso del crisotilo, è stato mostrato come avvenga un riscaldamento primario dell’ossido di calcio che porta a una successiva trasmissione del calore al resto del MCA, con la conseguente degradazione delle fibre (Yoshikawa et al. 2015).
Malgrado le evidenze scientifiche dimostrino la fattibilità di una inertizzazione dell’amianto basata sulle microonde, non risultano significativi utilizzi di questa tecnica su scala industriale. La ATON HT (Polonia, http://aton.com.pl/) detiene una domanda di brevetto internazionale (US2012/0024990) per l’uso delle microonde in presenza di additivi quali silicato di sodio e/o potassio, soda caustica e borace. Il processo è descritto nel dettaglio nella Relazione sull’analisi della filiera.
Trattamenti con ossidrogeno
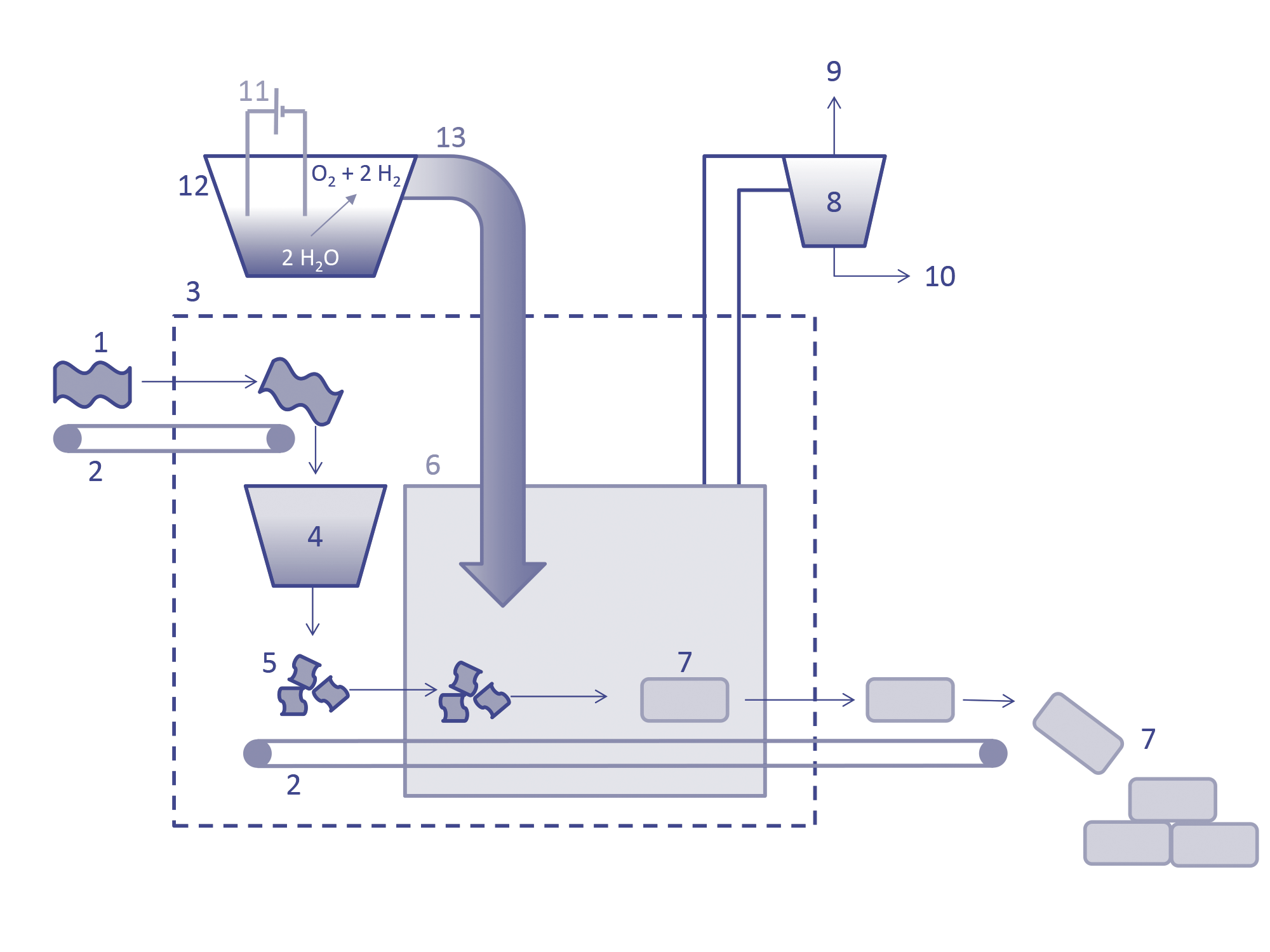
Schema del trattamento termico di MCA con ossidrogeno, ingresso MCA grezzi (1), nastri trasportatori (2), zona di bassa pressione (3), frantoio (4), MCA frantumato (5), zona ad alta temperatura (6), materiale inerte (7), sistema di abbattimento delle emissioni (8), emissioni di gas di scarico nell’atmosfera (9), ceneri (10), fonte di alimentazione (11), serbatoio di reazione dell’elettrolisi dell’acqua (12) e sistema di iniezione di gas di ossigeno secco (13).
Una strategia alternativa per raggiungere elevate temperature in prossimità dell’amianto è l’uso di una miscela gassosa stechiometrica 1:2 di ossigeno e idrogeno (ossidrogeno) derivante dall’elettrolisi dell’acqua. La successiva reazione tra i due componenti si innesca spontaneamente a 570 °C e rilascia un’energia di 241.8 kJ per mole di idrogeno. Con questa tecnologia è possibile raggiungere la temperatura di 2800 °C. Lo svantaggio di questa metodologia è ovviamente la bassa efficienza energetica del processo, in cui l’energia elettrica è consumata per l’elettrolisi dell’acqua per produrre la miscela gassosa.
Tale metodologia permette di degradare l’amianto con efficienza fino al 99% (Min et al., 2008), e un esempio di applicazione reale dell’ossidrogeno nella degradazione dell’amianto è costituito dal processo Cynergi, descritto nel dettaglio nella relazione sull’Analisi della Filiera.
Le Tecnologie Chimiche
I trattamenti chimici hanno lo scopo di distruggere le fibre di amianto attraverso attacco chimico ottenuto avvalendosi di acidi o basi forti concentrate e successiva neutralizzazione della miscela ottenuta finalizzata a estrarre prodotti riutilizzabili come inerti. Si tratta di applicazioni che in genere richiedono temperature di processo meno elevate dei processi termici ma comunque superiori a quelle ambientali. Il rischio dei trattamenti chimici è che l’inertizzazione avvenga solo a livello superficiale e non interessi le fibre localizzate nella parte più interna della struttura, che potrebbero essere rilasciate in seguito a una rottura del materiale prodotto.
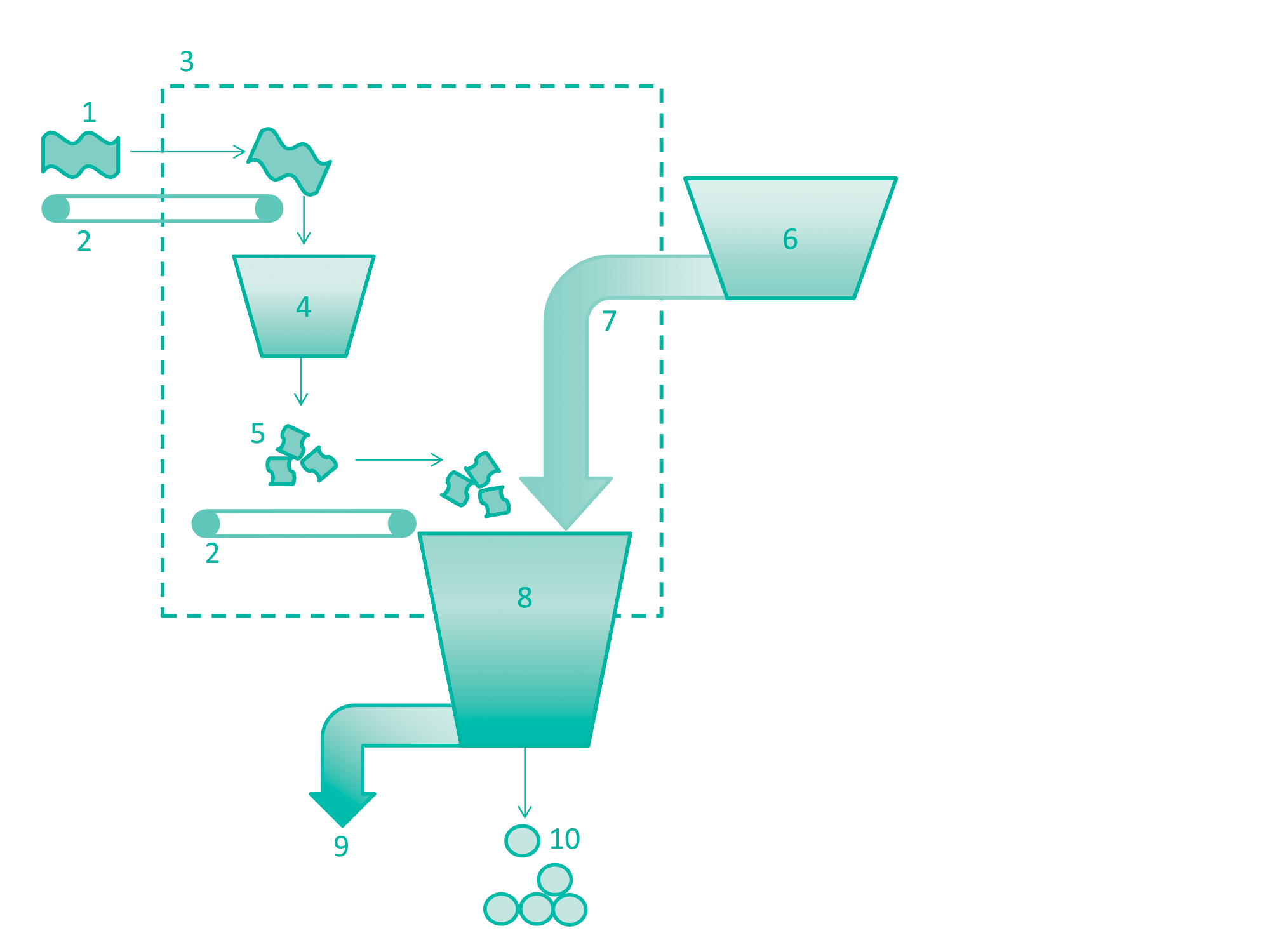
Diagramma di flusso del trattamento chimico di MCA, ingresso MCA grezzi (1), nastri trasportatori (2), zona di bassa pressione (3), frantoio (4), MCA frantumato (5), serbatoio di stoccaggio di sostanze chimiche (6 ), sistema di iniezione di sostanze chimiche (7), serbatoio di reazione (8), uscita dell’acqua di scarico (9) e residuo solido (10).
Trattamenti chimici classici (subcritici)
Essendo necessario idrolizzare il legame ossigeno-silicio, le due principali strategie sono:
• uso di pH altamente basici ( o più raramente acidi) che degradano la struttura dell’amianto generando silanoli liberi. A puro titolo di esempio, questa tecnica è stata proposta della WASTE TREATMENT BELGIUM (WTB) che a tale riguardo detiene anche un brevetto internazionale n. W097/00099
• uso dell’acido fluoridrico per formare fluoruro di silicio. A puro titolo di esempio, questa tecnica è stata proposta dalla SOLVEY UNWELTECHNIK Gmbh.
In generale, per poter ottenere risultati soddisfacenti, è necessario operare a temperature prossime ai 100 °C. Gli svantaggi di entrambe le tecniche sono legati ai costi legati al consumo dei reattivi e al successivo smaltimenti dei reflui.
Sia nel caso dei trattamenti basici che nel caso dei processi con acido fluoridrico, esistono brevetti per il loro utilizzo ma non sono note applicazioni reali a livello industriale. Una importante eccezione è rappresentata dalla statunitense KAI Technologies, il cui processo “ABCOV” utilizza un reattivo acido successivamente neutralizzato con sodio silicato e calce. Il processo utilizzato dalla Asbestos Conversion System utilizza una soluzione alcalina al 5-7% di borace, ma nel complesso va considerato come un processo termico e come tale è stato già descritto nel paragrafo 2.2 (trattamenti termici con ricristallizzazioni controllate).
Nella relazione sull’Analisi della filiera sono descritti nel dettaglio i seguenti processi che fanno uso delle metodologie appena descritte:
TRESENERIE
DENOMINAZIONE | DESCRIZIONE GENERALE | CARATTERISTICHE TECNICHE | FASI DEL PROCESSO |
TRESENERIE
PAESE: Belgio BREVETTO EUROPEO: WO 199700099 A1 TITOLARE: WASTE TREATMENTE BELGIUM (WTB) INVENTORE: Gérard Debailleul RICHIEDENTE: CLAEYS, P. etc LICENZA: – DATA DI PRIORITÀ: 16/06/1995 DATA DI DEPOSITO: 10/06/1996 DATA DI PUBBLICAZIONE: 3/01/1997 |
· Trattamento chimico basico inizialmente proposto per soli prodotti floccati e successivamente esteso alla tipologia del cemento-amianto.
Il processo, della durata di 20/30 minuti, si basa sulla dissoluzione delle fibre di amianto in una soluzione basica concentrata ed acquosa (> 25 moli/litro, 25 M) di idrossido di sodio (NaOH) o di potassio (KOH) contenuta all’interno di un reattore, ad una temperatura relativamente moderata e variabile tra i 160 ed i 175 °C, preferibilmente 170 °C e ad una pressione bassa compresa tra i 8 ed i 10 kg/cm2. Il materiale ottenuto viene inviato ad una centrifuga. La centrifugazione implica così una separazione solido-liquida che produce liquidi, i quali possono essere nuovamente rigenerati per costituire la nuova fase di attacco basico ed una fase solida (precipitato) concentrata e ridotta del 70% in volume rispetto alla prima fase, che può essere recuperata, introdotta in un secondo reattore supplementare ed attaccata basicamente per una seconda volta ad una temperatura più elevata della precedente, compresa tra i 190 ed i 210 °C, preferibilmente intorno ai 200 °C e ad una pressione tra i 2 ed i 10 kg/cm2, preferibilmente tra 2,5 e 5 kg/cm2. Questo secondo trattamento comporta la completa dissoluzione delle fibre. Il tutto viene inviato ad una seconda centrifuga, raffreddato ad una temperatura inferiore ai 180 °C e nuovamente separato. Il primo reattore è mobile e posizionato su un carrello, in modo da poter essere trasportato ed è chiuso per impedire la dispersione verso l’esterno delle fibre amiantifere. Il secondo reattore è fisso.
|
CATEGORIA: chimico.
SOTTOCATEGORIA: trattamento chimico classico con soluzione basica. TEMPERATURA DI TRATTAMENTO: 160-210 °C. STATO OPERATIVO: impianto pilota. MOBILITÀ: fisso o mobile. ALIMENTAZIONE: elettrica TIPO DI RCA TRATTABILE: friabili e compatti. PRETRATTAMENTO: nessuno. MATERIALE INERTIZZATO: prodotto diverso in relazione alla tipologia di amianto che viene trattata e può essere costituito da silice, silicati di diversi ossidi ed idrossidi di ferro. Quest’ultimi possono essere utilizzati come flocculanti di metalli pesanti nelle acque industriali o nelle soluzioni idro-metallurgiche. TRATTAMENTO REFLUI ED EMISSIONI: per evitare la formazione di gas pericolosi è prevista l’immissione di alluminio e zinco. |
· macinazione ad umido dei RCA; miscelazione in una soluzione acquosa (concentrata > 25 moli/litro) basica di NaOH o di KOH ad una temperatura tra i 160 ed i 210 °C e pressione tra gli 8 e i 10 bar;
· centrifugazione e conseguente separazione solido-liquida; · miscelazione in un secondo reattore con la fase liquida riciclata e rigenerata dalla centrifugazione ad una temperatura più elevata della precedente, compresa tra i 190 ed i 210 °C e ad una pressione tra i 2 ed i 10 kg/cm2; · estrazione dei materiali trattati. |
Wasteless Method
DENOMINAZIONE | DESCRIZIONE GENERALE | CARATTERISTICHE TECNICHE | FASI DEL PROCESSO |
WASTE-LESS-METHOD
PAESE: Polonia BREVETTO POLACCO: domanda n° P-359958 TITOLARE: Trefler B., Adam Pawelczyk A., Nowak M., Czarny A., Paszek A. e Zwodziak J. INVENTORE:- MANDANTE:- LICENZA:- ALTRE PUBBLICAZIONI: Pawelczyk A., Szczygiel B. (2009) – Prospects for processing wastes into products used in agricolture, Department of Chemistry, Wroclaw University of Technology, Wroclaw, Poland |
Processo di digestione dei minerali fibrosi con una soluzione di acido fosforico (H3PO4) fortemente concentrata costituito da due stadi.
I materiali trattati vengono appositamente macinati con aggiunta di acqua e successivamente inviati alla prima fase di digestione. In questo step la digestione acida porta alla formazione di una soluzione contenente fosfati ed un residuo solido contenente materiali silicei con eventuali fibre di amianto. Tale materiale solido viene separato per filtrazione da una soluzione liquida che viene ulteriormente neutralizzata con calce (CaO), mentre il residuo solido viene digerito con acido fosforico aggiunto in eccesso. Nel secondo step l’acido fosforico viene aggiunto in abbondante quantità in modo tale che l’eccesso venga inviato alla prima digestione acida. Dalla seconda digestione si ottiene silice per filtrazione e successivo lavaggio in acqua, mentre dalla neutralizzazione e successiva essiccazione si ottengono fertilizzanti fosfatici e concimi utilizzabili in agricoltura quali TSP (perfosfato triplo) e DCP (fosfato dicalcio) o ancora foraggio fosfato (MCP o fosfato monocalcico, LUB e DCP o fosfato dicalcico). L’intero processo è condotto ad una temperatura di 95 ºC per un tempo di circa 1 ora. Il residuo che non ha reagito durante le due fasi viene prima filtrato e successivamente reinserito all’interno dei digestori per completare l’opera di inertizzazione. |
CATEGORIA: chimico.
SOTTOCATEGORIA: trattamento subcritico con un acido forte. TEMPERATURA DI TRATTAMENTO: 80 °C (ottimale). STATO OPERATIVO: laboratorio. MOBILITÀ: fisso o mobile. TIPO DI RCA TRATTABILE: amianto e laste in cemento-amianto. PRETRATTAMENTO: – macinazione ad umido dei RCA. MATERIALE INERTIZZATO: ottengono fertilizzanti fosfatici e concimi utilizzabili in agricoltura quali TSP (perfosfato triplo) e DCP (fosfato dicalcio) o ancora foraggio fosfato (MCP o fosfato monocalcico, LUB e DCP o fosfato dicalcico). TRATTAMENTO REFLUI ED EMISSIONI: aspirazione dei vapori acidi con sistema di filtrazione e lavaggio. |
· macinazione ad umido dei RCA;
· prima digestione acida con formazione di una soluzione contenente fosfati ed un residuo solido contenete materiali silicei con eventuali fibre di amianto; · filtrazione del materiale solido; · neutralizzazione della soluzione liquida con calce (CaO); · seconda digestione acida del residuo solido con acido fosforico aggiunto in eccesso. |
ABCOV
DENOMINAZIONE | DESCRIZIONE GENERALE | CARATTERISTICHE TECNICHE | FASI DEL PROCESSO |
ABCOV
PAESE: Stati Uniti BREVETTI STATUNITENSI: US 5041277 A US 5258562 A US 5258131 A US 5264655 A BREVETTO EUROPEO: CA 2060500 C TITOLARE: William Mirick, Walter B. Forrister INVENTORE: William Mirick, Walter B. Forrister RICHIEDENTE: Austen-Chase Industries Inc., New York LICENZA:- DATA DI PRIORITÀ: – DATA DI DEPOSITO: 5/10/1992 DATA DI PUBBLICAZIONE: 23/11/1993
|
· Trattamento chimico che prevede un primo lavaggio con una soluzione acquosa contenente tra l’1 ed il 10% in peso di un acido organico debole.
· Il processo può essere utilizzato direttamente in situ “spruzzando” la soluzione contenente l’acido debole sui MCA in modo da inumidire le eventuali polveri generate dallo spostamento degli stessi, oppure immergendo questi ultimi in container contenenti la soluzione del trattamento. Si ritiene opportuno applicare la stessa soluzione acida due o più volte, in modo tale da aumentare fino al 98% la possibilità di conversione dei minerali. Successivamente si applica al materiale trattato, consistente in particelle amorfe simili chimicamente e strutturalmente a granelli di sabbia ed innocue, un agente stabilizzante, rappresentato da una resina, ad esempio lattice, in combinazione con materiali silicatici, con lo scopo di legare tra loro le particelle e prevenirne così l’aerodispersione. Al fine di incrementare il processo di bagnatura generalmente viene aggiunto alla soluzione acida un “wetting agent”, ossia un agente con lo scopo di ridurre la tensione superficiale. La conversione cristallochimica varia in tempo ed in successo a seconda dell’acido scelto e della sua concentrazione e può andare dai 2 giorni alle 4 settimane a causa della lentezza della reazione chimica. In collaborazione con Walter B. Forrister, nel 1993, è stato ottimizzato il processo, con il brevetto statunitense n° US 5258562 A. La novità del trattamento prevede una sorgente di ioni fluoruro, in una percentuale variante tra l’1 ed il 10% in peso, con lo scopo di accelerare il processo di conversione delle fibre di amianto. Un leggero riscaldamento ad una temperatura compresa tra i 50 e gli 80 °C può favorire, inoltre, il processo di inertizzazione dei MCA. Un ulteriore approfondimento del processo è stato effettuato nei successivi brevetti n° US 5258131 A e n° US 5264655 A, dove viene tra l’altro analizzato lo smaltimento delle sostanze risultanti dal trattamento acido. |
CATEGORIA: chimico.
SOTTOCATEGORIA: trattamento subcritico con un acido debole organico. TEMPERATURA DI TRATTAMENTO: 80 °C. STATO OPERATIVO: impianto pilota. MOBILITÀ: fisso o mobile. ALIMENTAZIONE: elettrica. TIPO DI RCA TRATTABILE: friabili e compatti. PRETRATTAMENTO: – spruzzatura dei RCA con un acido organico debole; – macinazione ad umido. MATERIALE INERTIZZATO: amorfi vetrosi, come fibre di vetro sottili, mentre una sostanziale porzione si dissolve e forma composti come l’acido fluorosilicico. Tali materiali presentano ottime proprietà isolanti e di ritardanti di fiamma. TRATTAMENTO REFLUI ED EMISSIONI: utilizzo di additivi alcalini quali idrossido di sodio, bicarbonato di sodio od idrossido di calcio. Tali composti si legano con i rimanenti ioni fluoruro dando vita al fluoruro di calcio, il quale è insolubile in acqua. Un’altra soluzione è quella di aggiungere alla miscela acida una percentuale compresa tra il 20 ed il 50% in peso di etanolo in modo da aumentare il livello di evaporazione. |
· spruzzatura dei RCA con un acido organico debole;
· macinazione ad umido; · ripetuti bagni in soluzione acida; · aggiunta di ioni fluoruro; · aggiunta di un agente stabilizzante; · filtrazione e separazione solido-liquido; · recupero prodotti amorfi vetrosi per l’industria. |
SOLVAS
DENOMINAZIONE | DESCRIZIONE GENERALE | CARATTERISTICHE TECNICHE | FASI DEL PROCESSO |
SOLVAS
PAESE: Germania BREVETTO EUROPEO: – TITOLARE: SOLVAY UMWELTTECHNIK Gmbh INVENTORE: – RICHIEDENTE: – LICENZA: – DATA DI PRIORITÀ: – DATA DI DEPOSITO: – DATA DI PUBBLICAZIONE: –
|
· Processo che consiste nella dissoluzione delle fibre di amianto con acido fluoridrico (HF).
· Un’unità pilota dalla capacità di 2 ton/g è stata realizzata nel 1992 a Brema, in un sito di stoccaggio di rifiuti di amianto ed è costituita da tre sezioni. La prima, in cui l’amianto viene preparato, è detta “zona nera”. In questa sezione in depressione l’amianto viene prima granulato e poi trasferito nella seconda sezione dove subisce un trattamento con acido fluoridrico. La reazione, che viene fatta avvenire con eccesso di acido, è fortemente esotermica e la temperatura di reazione può raggiungere i 100 °C. L’ultima fase del processo prevede l’utilizzo di latte di calce al fine di neutralizzare completamente la soluzione acida. Il calore che si genera viene disperso mediante uno scambiatore di calore di grande potenza. La neutralizzazione dell’acido in eccesso porta alla precipitazione di diversi composti degli elementi chimici presenti negli MCA (magnesio, ferro ecc.) quali fluoruri di calcio, ossidi ed idrossidi. Si separa così la fase liquida da quella solida e si realizza una polvere fine ed inerte utilizzabile per calcestruzzi, prodotti contenenti fluoro, fondenti e come materia base per la produzione di acido solforico. A fine trattamento i gas prodotti vengono convogliati verso un dispositivo di filtrazione e lavaggio, con controllo della concentrazione degli ioni fluoruro. Le soluzioni residue vengono trattate con idrossido di calcio, per neutralizzare e far precipitare il fluoruro di calcio e quindi riciclare la soluzione ai fini della produzione di acido fluoridrico. |
CATEGORIA: chimico.
SOTTOCATEGORIA: trattamento subcritico con un acido forte. TEMPERATURA DI TRATTAMENTO: 100 °C. STATO OPERATIVO: impianto pilota dalla capacità di 2 ton/g realizzato nel 1992 a Brema. MOBILITÀ: mobile. ALIMENTAZIONE: elettrica. TIPO DI RCA TRATTABILE: friabili e compatti. PRETRATTAMENTO: – macinazione dei RCA ad umido. MATERIALE INERTIZZATO: fluoruri ed esafluoruri degli elementi costituenti il materiale in ingresso ed in particolare da esafluorosilicati di Mg, Na e Fe, che possono essere impiegati come fondenti nell’industria del vetro e del cemento, in percentuali dell’1 e 2%. TRATTAMENTO REFLUI ED EMISSIONI: – |
· macinazione dei RCA in zona mantenuta in depressione;
· miscelazione con HF; · neutralizzazione della soluzione acida mediante latte di calce con precipitazione di fluoruro di calcio, idrossidi di Mg e Fe ecc…; · raffreddamento mediante uno scambiatore di calore; · filtrazione e separazione solido-liquido; · recupero prodotti per l’industria. |
Trattamento idrotermico (supercritico)
Un trattamento chimico che elimina il problema della gestione di reattivi corrosivi/pericolosi è il “trattamento idrotermico” (Anastasiadou et al., 2010), che prevede l’impiego di acqua supercritica a 250 MPa e 650 °C. In tali condizioni, lo stato fisico dell’acqua è quello di fluido supercritico. Questo approccio permette di operare a pH neutro. Il processo è stato sviluppato da Ssistemi, Politecnico di Milano e Università di Genova. Al momento la tecnologia è a livello prototipale. Le principali criticità legate al processo sono:
• le pressioni particolarmente elevate
• la filtrazione dell’acqua ottenuta
• la necessità (in alcune applicazioni specifiche) di aggiungere il 6% di acqua ossigenata
Per quanto riguarda la necessità di aggiungere un agente idrolitico ulteriore, si segnala che la Chemical Center ha un brevetto europeo in cui si utilizza il potenziale acido del siero di latte. In una prima fase viene separata una fase liquida acida e una fase solida contenente l’amianto, tramite solubilizzazione della componente cementizia. In una seconda fase, le fibre di amianto sono distrutte mediante processo idrotermale in siero di latte a temperatura e pressione elevate ad una temperatura da 120 a 250 °C e ad una pressione da 5 a 20 bar.
I processi idrotermici descritti nel dettaglio nella relazione sull’analisi della filiera sono:
S-SISTEMI UNI GE
DENOMINAZIONE | DESCRIZIONE GENERALE | CARATTERISTICHE TECNICHE | FASI DEL PROCESSO | |
S-SISTEMI UNI GE
PAESE: Italia BREVETTO ITALIANO: VI2005A000174 BREVETTO EUROPEO: EP 2038019 A1 BREVETTO STATUNITENSE: US 20100234667 A1 TITOLARE: – INVENTORE: Alberto Servida, Alessandro Servida, Simona Grassi e Giuseppe Nano RICHIEDENTE: Alberto Servida, Alessandro Servida, Simona Grassi e Giuseppe Nano LICENZA: – DATA DI PRIORITÀ: – DATA DI DEPOSITO: 20/06/2006 DATA DI PUBBLICAZIONE: 16/09/2010 |
Processo idro-termico con pre-triturazione grossolana in presenza di acqua, al fine di ottenere una pasta che abbia un contenuto di materia solida compreso tra il 20 ed il 50%, preferibilmente non superiore al 30% in peso.
Il metodo prevede l’aggiunta alla fase acquosa di un composto ossidante, in una predeterminata concentrazione, come ad esempio il perossido di idrogeno. Altri composti ossidanti sono l’ossigeno, l’ossigeno arricchito di aria, l’aria e l’ozono, quest’ultimo prodotto direttamente sul sito tramite un ozonizzatore. Essi vengono aggiunti prima che la fase acquosa venga sottoposta a riscaldamento, in una concentrazione che varia a seconda del composto scelto, compresa tra l’1 ed il 10%, preferibilmente tra l’3 ed il 6% in peso. Il perossido d’idrogeno viene aggiunto in una concentrazione compresa tra l’1 ed il 10% in peso, mentre l’ossigeno tra lo 0,4 ed il 4%. Il tutto viene poi caricato all’interno di un reattore e sottoposto alla fase acquosa supercritica ad una pressione compresa tra i 25 ed i 27 MPa e ad una temperatura che varia tra i 600 ed i 650 °C. Segue il raffreddamento e la condensazione della fase acquosa uscente dal reattore e la separazione dei residui solidi. Il tempo del trattamento va dai 30 ai 180 minuti. |
CATEGORIA: chimico.
SOTTOCATEGORIA: trattamento idro-termico con acqua supercritica. TEMPERATURA DI TRATTAMENTO: 600-650 °C. STATO OPERATIVO: laboratorio. MOBILITÀ: fisso o mobile. ALIMENTAZIONE: elettrica. TIPO DI RCA TRATTABILE: RCA in matrice organica ed inorganica, ma anche semplicemente fibre di amianto. PRETRATTAMENTO: – triturazione grossolana ad umido dei RCA. MATERIALE INERTIZZATO: inerti solidi, quali silicati di Mg e/o Ca, silice, acqua ed anidride carbonica senza l’utilizzo di reagenti dannosi. TRATTAMENTO REFLUI ED EMISSIONI: – |
· triturazione grossolana ad umido dei RCA;
· carico nel reattore; · pressurizzazione a 25-27 MPa; · inserimento nel forno elettrico a letto fluidizzato; · raffreddamento e condensazione del fluido estratto dal reattore; · filtraggio della soluzione condensata e separazione dei residui solidi. |
CHEMICAL CENTER
DENOMINAZIONE | DESCRIZIONE GENERALE | CARATTERISTICHE TECNICHE | FASI DEL PROCESSO |
CHEMICAL CENTER
PAESE: Italia BREVETTO ITALIANO: MI2010A001443 BREVETTO EUROPEO: EP 2428254 A1 TITOLARE: Chemical Center S.r.l. INVENTORE: Marco Lelli, Giorgio Isidoro Lesci, Marco Marchetti, Filippo Pierini e Norberto Roveri RICHIEDENTE: Cristina Biggi LICENZA: – DATA DI PRIORITÀ: 30/07/2010 DATA DI DEPOSITO: 26/07/2011 DATA DI PUBBLICAZIONE: 27/03/2013
|
· Processo che accoppia ad un trattamento idro-termico un trattamento acido mediante un prodotto di scarto industriale acido, il “siero di latte esausto”, il quale oltre a creare un ambiente acido, apporta componenti batteriche che si ritiene favoriscano l’attacco del materiale stesso.
· Nel caso in cui si utilizzino materiali contenenti amianto in matrici compatte non cementizie viene preferibilmente attuato un pretrattamento termico che comporta la combustione della matrice ed il rilascio delle fibre. Tali rifiuti vengono trasportati avvolti con una pellicola protettiva. Il materiale avvolto in tale pellicola ed immerso in una vasca contenente siero di latte viene così sottoposto a frantumazione. · Questa fase viene condotta in vasca chiusa così da poter raccogliere e convogliare la CO2 che si sviluppa in un impianto di utilizzazione della stessa senza emissione in atmosfera. Le fibre residue del trattamento col siero esausto, previa filtrazione, vengono aspirate e convogliate in un reattore idro-termico (preferibilmente in acciaio) ed in seguito distrutte completamente a temperature da 120-150 °C, ad una pressione compresa tra i 5 e i 20 bar e per un tempo variabile dalle 12 alle 168 ore. A termine di tale operazione si ottiene una fase solida costituita essenzialmente da silicati ed ossalati insieme ad una componente organica risultante dalla trasformazione termica della componente batterica e di una fase liquida che risulta ricca di differenti ioni metallici. · Al fine di favorire il passaggio di fase da amianto a composti inorganici non tossici durante il trattamento idro-termico è opportuno aggiungere almeno un agente chelante. Si ritiene che la chelazione degli ioni Mg delle fibre promuova lo sfaldamento dei piani cristallini del crisotilo. |
CATEGORIA: chimico.
SOTTOCATEGORIA: trattamento idro-termico in bagno acido con siero di latte. TEMPERATURA DI TRATTAMENTO: 120-250 °C. STATO OPERATIVO: laboratorio. MOBILITÀ: fisso o mobile. ALIMENTAZIONE: elettrica. TIPO DI RCA TRATTABILE: i materiali trattati possono essere sia in forma fibrillare, in matrici friabili oppure in matrici cementizie, od anche in matrici compatte di tipo polimerico (polimeri sintetici o cellulosici). PRETRATTAMENTO: – pretrattamento termico in caso di matrici polimeriche. MATERIALE INERTIZZATO: – ossalati, carbonati e silicati derivanti dal trattamento idro-termico utilizzabili nell’industria ceramica; – residui batterici derivanti dal trattamento idro-termico come fertilizzanti agricoli; – soluzione acquosa derivante dal trattamento idro-termico costituita da ioni metallici ricca in Mg, Ni, Mn, K, Fe e Ca, da cui possono essere estratti tramite processi elettrolitici i vari metalli elementari. TRATTAMENTO REFLUI ED EMISSIONI: – liberazione di CO2. |
· macinazione dei MCA in soluzione di siero di latte con pH compreso tra 2 e 6;
· aggiunta di acidi organici per ottenere un pH tra 1 e 3; · miscelazione in soluzione acida per 12-120 ore ad una temperatura tra 30 e 90 °C; · trattamento idro-termico per 72-120 ore alla temperatura di 120-250 °C e alla pressione di 5-20 bar; · raffreddamento; · estrazione del materiale trattato. |
Trattamento con agenti riducenti
I silicati come l’amianto possono essere degradati tramite reazione con un opportuno agente riducente. Il processo richiede l’aggiunta di un riducente come un metallo allo stato elementare (che determina il costo totale del processo). Altra criticità di questi processi è legata all’innesco della reazione. Il vantaggio di questo approccio è che le reazioni di ossidoriduzione sono favorite e una volta avviate procedono spontaneamente. Si parla a tal proposito di self-propagating high temperature syntheses.
Ad esempio, è stato mostrato come l’amianto degradato con una miscela di ossido ferrico e magnesio elementare (Porcu et al., 2005). Un ulteriore esempio di trattamento chimico basato sull’ossidoriduzione dei silicati in presenza di alluminio è alla base del progetto dell’Università di Genova LIFE FIBERS (LIFE12 ENV IT 000295), descritto nel dettaglio nella relazione sull’Analisi della filiera.
Le Tecnologie meccanochimiche
I trattamenti meccanochimici affidano all’energia meccanica trasmessa al MCA da macchine trituratici il compito di distruggere i reticoli cristallini ed i legami molecolari presenti nell’amianto, causa della sua stessa pericolosità (Plescia et al., 2003).
I processi di macinazione ad alta energia od ultramacinazione sono stati proposti e utilizzati con successo alla scala di laboratorio e reale per trattare i RCA. Nello specifico è stato dimostrato che la macinazione di fillosilicati, che avviene in mulini che operano con le più diverse metodologie, ne determina la progressiva amorfizzazione grazie al rilascio degli ioni ossidrile necessari al mantenimento della struttura cristallina. Si parla anche di “vetrificazione a freddo”.
Sono state eseguite delle sperimentazioni sul minerale proveniente da Balangero ed al termine del procedimento è risultato praticamente puro.
Un campione di crisotilo, ad esempio, è stato macinato per 4, 8, 12, 16 e 20 minuti in un mulino Herzog HSM 100, con una proporzione di 1:100 rispetto alla massa macinante. Dopo pochi minuti di trattamento non si è più riscontrata la presenza di fibre, mentre dal punto di vista cristallografico il materiale prodotto non è più individuabile come amianto. Le sollecitazioni meccaniche, imposte per compressione e sfregamento, portano ad una rapida distorsione reticolare, ad una espulsione delle molecole d’acqua, OH e CO2 ed alla formazione di un materiale isotropo e amorfo.
I test di laboratorio evidenziano come tale trattamento sia efficace anche se con tempi differenti, dagli 8 minuti del crisotilo ai 12 degli anfiboli.
Il processo analizzato che prevede l’utilizzo di questo trattamento è il seguente:
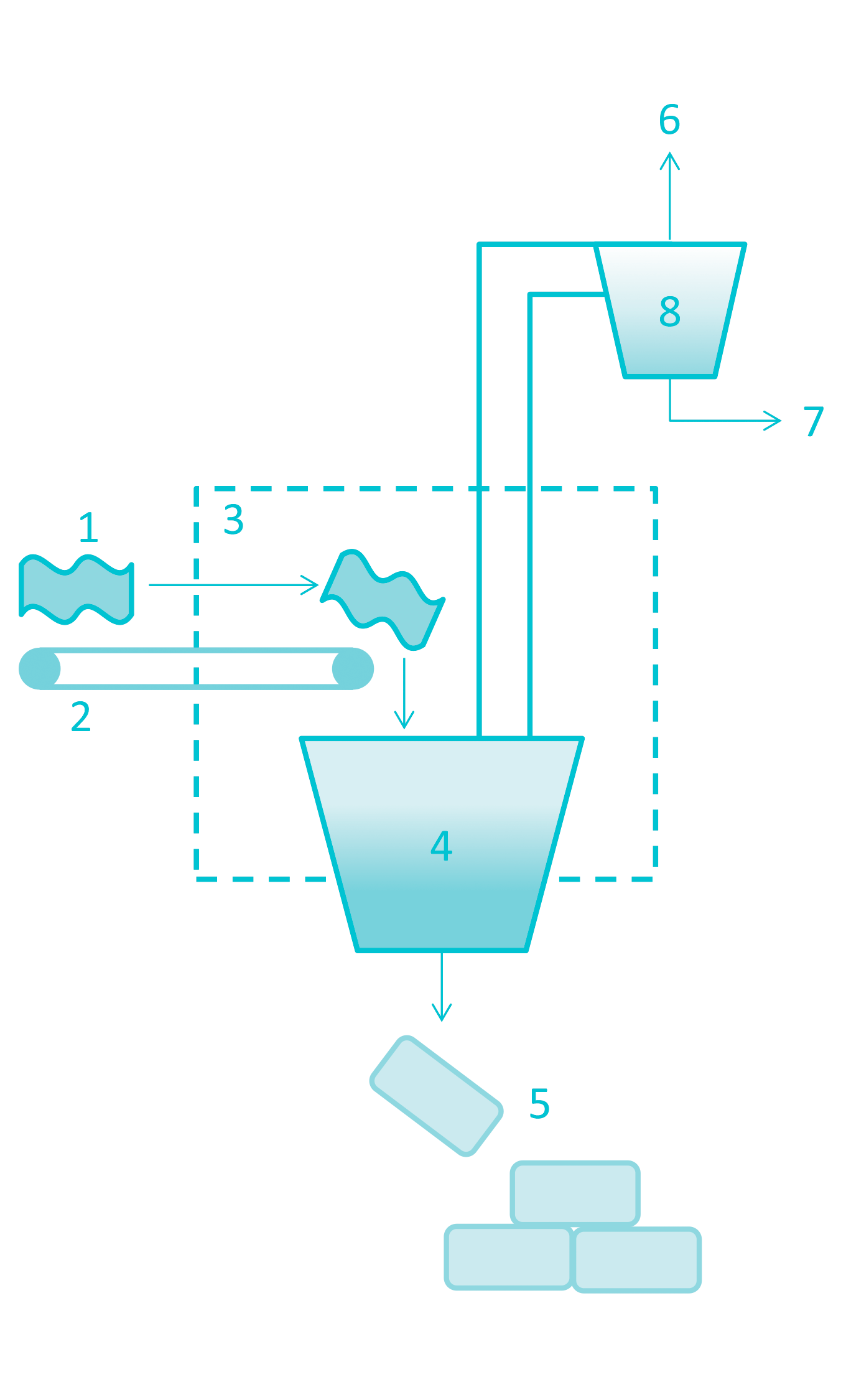
Diagramma di flusso del trattamento meccanochimico di MCA, ingresso MCA grezzi (1), nastro trasportatore (2), zona di bassa pressione (3), mulino ad alta efficienza (4), materiale inerte (5), emissioni di gas di scarico nel atmosfera (6), ceneri (7) e sistema di abbattimento delle emissioni (8).
HEM (HIGH ENERGY MILLING)
DENOMINAZIONE | DESCRIZIONE GENERALE | CARATTERISTICHE TECNICHE | FASI DEL PROCESSO |
HEM (High Energy Milling)
PAESE: Italia BREVETTO ITALIANO: – BREVETTO EUROPEO: – TITOLARE: – INVENTORE: F. Colangelo del Dipartimento di Tecnologia dell’Università Partenopea di Napoli, R. Cioffi, M. Lavorgna e L. Verdolotti dell’Istituto per i Materiali Compositi e Biomedici (IMCB) del CNR di Napoli e L. De Stefano dell’Istituto per la Microelettrica e i Microsistemi sempre del CNR di Napoli RICHIEDENTE: – LICENZA: – DATA DI PRIORITÀ: – DATA DI DEPOSITO: – DATA DI PUBBLICAZIONE: – |
Trattamento di macinazione dei RCA ad alta energia.
I RCA sigillati in sacchi di polietilene e parzialmente bagnati vengono aperti in una cappa a flusso laminare in modo tale da evitare l’aerodispersione delle fibre e successivamente, sempre sotto cappa, macinati a secco all’interno di un mortaio e ridotti a dimensioni millimetriche. Questi campioni vengono così trasferiti ad un mulino a sfere. La macinazione perdura per un tempo di circa due ore. I risultati delle analisi spettrofotometriche e diffrattometriche a raggi X effettuati sui rifiuti contenete amianto mostrano una totale trasformazione della struttura chimica e cristallina degli asbesti. |
CATEGORIA: meccano-chimico.
SOTTOCATEGORIA: trattamento di macinazione ad alta energia. TEMPERATURA DI TRATTAMENTO: – STATO OPERATIVO: – MOBILITÀ: – ALIMENTAZIONE: – TIPO DI RCA TRATTABILE: friabili e compatto, cemento-amianto. PRETRATTAMENTO: nessuno. MATERIALE INERTIZZATO: sottili polveri ottenute possono essere così riutilizzate in numerose applicazione di ingegneria civile come ad esempio nella produzione di materiali da costruzione come il cemento e le malte, avendo queste polveri un’ottima attività pozzolanica. Le caratteristiche meccaniche delle malte preparate con tali miscele risultano migliori di quelle preparate con calce e pozzolana. TRATTAMENTO REFLUI ED EMISSIONI: – |
· macinazione dei RCA ad alta energia;
· estrazione dei prodotti trattati. |